Joining me for Episode #265 of the podcast is Bernita Beikmann, AIA, EDAC, LSSBB, a Principal and Director of Lean Strategy at HKS, an international architecture firm.
Bernita is originally from Kansas and has a Bachelor of Architecture from Kansas State University and a Certificate in Regional and Community Planning. She moved to Dallas in 1996 and has been employed by HKS, Inc in Dallas since that time.
We first crossed paths when we had the opportunity to work together on a project for Riley Hospital for Children in Indianapolis to work with staff and leaders on designing parts of a new patient tower. You can read a bit about that work here. You might also remember her guest post on the blog from 2013. I hope you enjoy our conversation.
Streaming Player
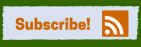
For a link to this episode, refer people to www.leanblog.org/265.
Topics and Links for this episode:
- How did you get introduced to Lean?
- What process do you use with clients for “Lean Design” or “Lean Project Delivery?”
- How is it different than the “traditional model?”
- What are some of the successes you've seen?
- The role of the construction firm?
- Physical mockups vs. virtual reality technologies
- Reducing waste instead of “stripping out cost”
- Breaking down silos
- Chicken and the egg – is it necessary (or helpful) to have a Lean program before a Lean Design effort, or vice versa?
- The book The Toyota Way
- Lean Construction Institute
- Book — Lean Operations, Lean Design, Lean Construction: Building a Lean Hospital Facility (about work at Akron Children's Hospital)
- The new chapter on Lean Design from my book Lean Hospitals
For earlier episodes of my podcast, visit the main Podcast page, which includes information on how to subscribe via RSS, through Android apps, or via Apple Podcasts. You can also subscribe and listen via Stitcher.
Thanks for listening!
Past Post by Bernita Beikmann
Video with Bernita Beikmann
Transcript:
Announcer (42s):
Welcome to the Lean Blog podcast. Visit our website www.leanblog.org. Now, here's your host, Mark Graban.
Mark Graban (53s):
Hi, this is Mark Graban. Welcome to episode 265 of the podcast for October 12th, 2016. Joining me today is Bernita Biekmann. She is a principal and director of Lean Strategy at HKS, an international architecture firm. Bernita is originally from Kansas and has a bachelor of architecture degree from Kansas State University and a certificate in regional and community planning. She moved to Dallas in 1996, has been employed by HKS since that time. Now Bernita and I first crossed paths a few years ago. We had the opportunity to work together on a project for Riley Hospital for Children in Indianapolis, to work with staff and leaders on designing parts of a new hospital tower using lean principles, incorporating workflows, and lean design.
Mark Graban (1m 43s):
You can read a bit about that in a link that is on the page of this episode at leanblog.org/265. There are links to the Lean Construction Institute, the, the book, the Toyota Way that Bernita used originally to learn about Lean and a more recent book about the work at Akron Children's Hospital, a book called Lean Operations, lean Design, lean Construction Building a Lean Hospital Facility. And if you go to that page again leanblog.org/265, there's a link to download a PDF of the new chapter in the third edition of my book Lean Hospitals on these principles of lean design.
Mark Graban (2m 28s):
So I hope you enjoy the conversation, and as always, thanks for listening. Bernita Hi, thank you for being a guest on the podcast today.
Bernita Biekmann (2m 39s):
Thanks, Mark. It's good to be here.
Mark Graban (2m 41s):
So if you can, you know, start off, it'd be interesting to hear about some of your professional background and, and what you do and, and maybe also kind of then segue into, you know, how as an architect you first got exposed to Lean.
Bernita Biekmann (2m 57s):
So I will give you my Lean Life story. Probably about eight or nine years ago. I remember I had a, a child right before it, so that helps me remember the timeline. I had a client who requested that we transitioned a project from a traditional project structure to a lean project delivery method. And because of that, they, the client educated the entire team. We, you know, read Toyota, the Toyota Way together. We did some other studies together. We ended up completing that project using lean project delivery, tried to the way we do the work and I think opened the eyes of everyone on the team that even though we thought we were doing a great job, everyone was a, was a professional in their field and had good reputation as doing a great job that we could actually do better and not only by ourselves, but by our clients as well.
Bernita Biekmann (3m 59s):
So I did a little bit more education own and was fortunate enough to work on several other projects that were not only doing it for the design and construction delivery of the project, but also in their internal operations as well. So many healthcare systems who were looking at how they could actually deliver care differently, how they could improve both the patient experience and the staff experience within hospital facilities. So I started jumping in to getting a little bit deeper education myself, reading as much as I could, and every Lean Enterprise Institute class I could take.
Bernita Biekmann (4m 42s):
And then the last big education part was about years ago I completed my six sig just so that I not only could continue the work on projects, but also be a leader in my organization to actually do improvements within how we deliver projects regardless of delivery type and how we even treat our staff. So it's been a great experience for me to just improve myself and get the opportunity to improve my industry and my organization. Yeah,
Mark Graban (5m 20s):
And, and maybe if you can give a little bit of background, you know, to the, the type of work you do as an architect, how would you describe or compare and contrast, you know, what you called that traditional model for working with a client to a lean project delivery model. There might be listeners who don't know that term even, but I mean, how, how people who've never worked with architects and that redesign or construction process. How would you compare and contrast the old way and the lean way?
Bernita Biekmann (5m 51s):
So I probably didn't mention this, but I am an architect in the state of Texas. I've been a, with HKS 20 years. I have my 20 year anniversary in June. So most people I think have some kind of familiarity with a traditional construction process, whether they've had a, you know, a sidewalk port or new yard or a improvement done on their house. And, and usually the process is, is you either have an idea of what you want or you hire a design professional to help you with that idea of what you want, and you might have an agreement with that design professional.
Bernita Biekmann (6m 32s):
And then you independently hire construction professionals to build it. So right away you have two big, giant silos. You have the people that designed the project for you, and you have the people that are gonna build the project for you. And sometimes even people that are building the project, or most time the people that are building the project actually have multiple other contracts with other organizations that are doing, especially when you have a big project doing other pieces of the work. So if it's on your house, you might hire a, a general contractor to actually build your house, a renovator house, but they will still hire someone to do the floor, they'll hire someone to do the plumbing, they'll hire someone independently.
Bernita Biekmann (7m 17s):
So now we have even more silos of people who are doing work, not necessarily knowing what your vision is as a homeowner or a business owner, not understanding all of that, but they're all trying to perform the, trying to perform the work based on what they feel. So using lean actually aligns all those different groups to work together and it allows people to have a share of what, what the client and the end customer actually wants. It allows them to look at it from a different perspective and work together differently. So oftentimes projects that are delivered in a lean way, it's a team approach to delivering a project.
Bernita Biekmann (8m 1s):
You often get a better aligned vision to what you really want and you get that better aligned vision for a much better price and often with better quality just because you're removed all those separate silos and you allow people to work together in the, in the, in the best way possible.
Mark Graban (8m 20s):
So in the traditional model, I guess, you know, some of the point pain points for the, the client more specifically, it's not just the, I guess, you know, the, the the process pain point of they don't understand our vision or people are working in silos. Does that lead to, I guess, you know, the slow delivery, you know, missing deadlines going over cost, not, not quite translating the needs in, into what's actually built problems like that?
Bernita Biekmann (8m 49s):
Well, and if you think about just, just the, the simple contrast between something like single piece flow and batch flow, so single piece, the lean mindset actually creates the better opportunity for single piece flow because you all those different companies are, are brought together to create the best process initially to deliver the project in a way that's most cost effective and gets the best value. Whereas a traditional model, all I care about is my contractor, what I produce, and I'm gonna produce everything that I need to produce at the time that's convenient for me. So it's more of a, of a batch thrown into the system than it lands where it needs to land.
Bernita Biekmann (9m 31s):
And yes, there's coordination involved at, at some level, but the introduction of lean into that OV overall process helps create a, a better mindset to deliver that project more effectively.
Mark Graban (9m 51s):
I mean, part of what you're describing mean, it sounds like there's almost some good parallels to somebody trying to navigate the healthcare system as a patient. They may be dealing with a lot of individual silos and you know, like you said, everyone's individually doing their best or you know, trying to, you know, meet their own goals, but they're having to coordinate their own care. And is that addressed jumping back to architecture, you know, through this lean project delivery model of the client not being the only one who's trying to manage all the silos?
Bernita Biekmann (10m 27s):
Yeah, and I think, I think really there, there's a lot of really good parallels between the health street and design and construction. Most, like if you think about in terms of there's people that supply a product to a hospital and there's people just that distribute the product within the hospital, but really what the patient cares, cares about is, you know, getting equipment in the, in the medicine to make them feel better so that they can go home. So that's the most important part of that. But you have all these outside factors that are supplying these equipment and, and, and materials in different ways, and a lot of times those different systems don't even talk to each other or they've never even had a about how they're gonna work together. Right.
Bernita Biekmann (11m 7s):
And that's, that's really what we're doing by combining lean operations in, in lean design and construction is actually facilitating sessions where suppliers and equipment providers and staff and in a lot of cases, representation from patients and families have conversations about what is the best methods for a patient to receive care. And of course with staff in, in input as well as what is the safest way for them to deliver that care as well. And then facilitating an environment that supports that. So if I've decided for instance that the best, the best way to reduce errors and the best way to deliver patient care is by having, having medicine at the bedside.
Bernita Biekmann (11m 55s):
That means I'm gonna design a patient room in a different way and I will design medication rooms in a different way and I meet design storage rooms in a different way to actually gather the materials as they come into the building. So there's a direct correlation to the work that, that the operational improvement work that our clients do and the built environment and the built environment can support it in a way that allows for flexibility and can actually make it perform better operationally.
Mark Graban (12m 29s):
So I mean, you, you've touched on a little bit about how this process works of, you know, getting staff involved, understanding staff needs and, and what they want need to do with the patient. Can you maybe kind of step back and kind of walk through the lean project delivery model, if an organization is getting started in let's say, you know, a major redesign of a space or building a new tower or building a new site, can you kinda walk through how that process works at a high level? How do you help coordinate that as the architect?
Bernita Biekmann (13m 3s):
So usually the first question that we ask, and sometimes they, the organizations if they do have a lean operational improvement program in place already have a first step of this is we want them to understand how they're operating now and why they're operating way. Because a lot of times if we, if we walk like in a non-line design way, we'll walk in and offer solutions to problems they have without understanding what the problem is in the first place. So I might walk in and the easiest thing for me to pick on is, you know, works stations on wheels.
Bernita Biekmann (13m 44s):
I, the facility could tell me I hate workstations on wheels. And we could say, okay, well we just won't put, put them in the new facility and I'm gonna walk in day one and have design a patient floor that doesn't contain them. But we really want them to understand is how they're doing things now and why they're doing 'em that way. And then we wanna think about what their future state is gonna be understanding, understanding the cultural norms that they have in place in their community, understanding things that are, are out there as far as new trends or, or new technology. And start to think about what, what could be their ideal and what could be their future state.
Bernita Biekmann (14m 26s):
And then we'll often come and do presentations on, on trends that we're seeing in the industry, or we may take them on site tours of, of other facilities that are newer or that are, that have a model just to give them different ways to think about how facilities working are are working. Because sometimes, you know, if I've worked my entire career in a certain facility, I might not understand the possibilities that exist if the equipment was different or the technology was different or any number of factors. So we have, we have those initial discussions. We might do visioning sessions to, to understand what their, their vision and goals are for the new facility.
Bernita Biekmann (15m 11s):
And then we will usually take them on either a small or a large version of a three P process, which it production preparation process or people preparation process where we do rapid prototyping of different options for the design of a space. And it's very interactive. It could be, we use the staff as part of that, but it's, it's kind of rapid fire looking at different options and asking a lot of questions on adjacencies and, and overall space allocation for different possibilities.
Bernita Biekmann (15m 52s):
And a lot of times, we'll, we'll create either small versions of, you know, for instance, if we were doing a patient four, we might immediately start creating different mockups of that patient. But some facilities we've mocked up entire departments and we'll do that rapidly. We might look at three to four different mockups of their department in a week on period. And the way we can do that is because we make out of things like cardboard, four by eight sheets of cardboard can be configured easily. People can walk through it much like they would walk through something, you know, a month before they open and do day in the life training or they're doing initial training for, they do things like, okay, what happens in this room if there's a code and they run through that scenario.
Bernita Biekmann (16m 42s):
And, and what happens in this room if you need to do an actually a or procedure with an emergency procedure in this room? Do you have enough space? Do you have the right equipment? Do you have the right adjacencies to elevators or, or medicine or supplies? And that allows us to make, to observe and make adjustments to the plans to, before they actually even exist. So if you can think about that from a construction perspective, a lot of traditional projects will do that kind of training and do those kind of observations after the keys are turned over or one construction's about finished.
Bernita Biekmann (17m 28s):
We had one client who did that kind of training and ended up moving some rooms multiple times. They specifically moved their, moved their meds room three times before they opened, which costs hundreds of thousands of dollars for them to do that because they were about to open. Whereas we're doing this with cardboard, we can can rip it down and physically just move it over in the matter of the matter of an hour and then they can run that test again and see if they've actually improved their output. And you know, they, they, it's very effective in terms terms of staff understanding the space as well because a lot of times actually most times staff are not familiar with looking at drawings.
Bernita Biekmann (18m 15s):
So expecting them to understand much less comment on a two dimensional line drawing of a space is not nearly as effective as saying, you understand your job here it is in three dimensions to scale. Go take care of a patient and see if it works. And we're able to add details, make adjustments on the fly quite easily before we even draw anything. So beyond that then it even, I mean you can go into other, other layers of how we work with the design, the rest of the construction team where we might pull in the people that are actually building the, the drywall trades or the, the window trades that, that are actually building some of these things and having 'em come up with different ways for us to make adjustments to, to save cost on the project.
Bernita Biekmann (19m 5s):
And sometimes that saving cost on the project actually lets our clients maybe buy better equipment than they could before or maybe we're just making improvements for the physical environment that, so something like changing, you know, vinyl tile to rubber flooring, which is actually better for the staff that's walking on that long term and it's quieter for the patient. So there's, there's a lot of d grays we can do when we start pulling the normally siloed groups in and having honest discussions about how we build things and how how much things cost so that we can improve the value and quality of the overall project. So, so when you have a lot of information
Mark Graban (19m 45s):
Yeah, but you know, there's, you've, you've touched on a lot of the highlights and maybe we can come back and dig into some of those aspects a little bit more, but you know, you highlight, you know, the, the teamwork, the iterative process, you know, breaking down silos as you mentioned earlier. When, how does the role of the construction company change in this LPD process? Is, is it more collaborative with the construction company as opposed to, I don't know if this was the case in the past of doing the design and then kind of throwing it over the wall and saying, here you build it. Can you talk about some of the teamwork and collaboration that you would hope to see?
Bernita Biekmann (20m 25s):
So Yeah, absolutely. It is. It's traditionally, it's, it's pretty much we have to, the design professionals have to get to a certain point where the construction professionals, sometimes they comment on constructability, but most often it's cost and it's very much thrown over the wall, find out where we are, throw it back over in us oftentimes having to strip out things to get it into cost. So by inviting them into the process there, there may be small changes that we can make that don't affect operations, but that significantly change, change cost. So everything from, you know, reducing angled walls, reducing constructability, actually even sometimes improving the ability for the actual construction to be safer.
Bernita Biekmann (21m 16s):
There are things that we can do on how we detail different elements in the building to make it safer to construct so that they actually improve labor during construction, which overall can reduce cost. So it's, it's, it's fairly complex, but by working together with them, both from an estimating perspective and from a constructability perspective, there's a lot of improvements we can make as an industry that ultimately lead to our end customers getting more for their money. Right.
Mark Graban (21m 48s):
Well, and when you talk about getting more for their money, I think you've brought up this idea a couple times already. There's a big difference between, I think as you just put it, stripping out cost and reducing waste and, and saving money in a way that doesn't leave people feeling like they actually got less value from their, their building. That seems like a, a really nice common core lean principle there of reducing waste instead of just cutting costs. Is there anything you, you could say to elaborate on that idea?
Bernita Biekmann (22m 19s):
Well, and I think it's also giving the, the client and end users enough information to make the right decision. Because if, if I go and, you know, if I go and ask a nurse that's working in an ed, what kind of door do you want? They might pick the most, the most expensive door that's out there. So they might want an automatic glass slider that allows 'em to see in the room that has integral blinds and, and all this great stuff. If I ask them, compared to the cost of that door and this piece of equipment that allows you to, if we take the $5,000 of the door instead and apply it to the $5,000 piece of equipment that can provide better patient care, there's a greater chance that they would, they would pick the best thing for the patient.
Bernita Biekmann (23m 12s):
Now, in some cases it might be the door, but other cases it might be that piece of equipment. But us having those conversations in the, in the room about safety things for patients, better care safety things for staff gives them the right information to make this decision. Whereas sometimes if, if we can't include them because it's six months after the users are even involved, when we find out we have a cost issue, we might, the overall team might have to make hard decisions without that direct input and I would rather have their input on making those decisions.
Mark Graban (23m 50s):
Yeah. Well I mean it sounds like, is there a parallel to medicine where, you know, I think the old there, there's tension sometimes with the old model is the patient just tells the doctor, well, you tell me what to do, you're the expert as opposed to a model, a more engaged patient model of, you know, providing information alternatives to that patient, sometimes taking the financial considerations into account and, and letting the patient be more of a partner, helping the patient make that decision. That, that strikes me as similar to what you're describing is, is there sort of an old model where the client would say, for better or for worse, hey, you're the architect, you tell me how to do it, as opposed to collaborating.
Bernita Biekmann (24m 34s):
Right. And you know, we, we still see a little of that because there are still clients who are like, well, you're the experts, you know, we want, we want to the, the top of a line thing. But there are so many different facets to it. So much like you're, if if I can, if I can get staff buy-in to the space that's being designed and they have an understanding of why different decisions were made, there's a greater chance that they're gonna be happier in that space and they know where, they know why we made certain decisions. And the same thing with patient care. If I have an understanding of of, of what I'm getting certain medicines, what are they supposed to do for me, why I'm supposed to be, you know, doing the rehab and the benefits to me, there's a greater chance that I'm gonna take that medicine, I'm gonna do that rehab than I'm gonna actually participate in in my own, you know, wellness as opposed to just saying this stuff better work.
Mark Graban (25m 24s):
Yeah.
Bernita Biekmann (25m 26s):
So yeah, there's definite parallels between the two.
Mark Graban (25m 28s):
Yeah. Well, o one other thing, you know, kind of go back to some of your, your earlier points. You, you talked about healthcare organizations who have some form of a lean program and, and realizing that could mean a lot of different things in a spectrum of, of experience with lean or commitment to lean. Do you, do you see kind of a wide spectrum? Do do people tend to have a fairly advanced approach to lean, to be at a point where they're reaching out and asking for lean design? Or do you have people who are at earlier stages who maybe see this as a way of getting started and you know, within that spectrum, do you have any reflections on, I mean this isn't the the right way of asking the question of, you know, who, who is more successful with this lean approach to design and construction?
Bernita Biekmann (26m 23s):
I I think ideally they're all like deep into their journey that we can just support it. Right. But I will take anything Yeah. Or any, just the idea that an organization is, is trying to do their best to be better than they were yesterday is a good step in the right direction. And sure, it, It helps me do my job better for them to be, to be positive about thinking about how they do the work today and how they wanna do the work in the future. Because that's, that's a big stepping stone to get over because a lot of organizations are just fix, just fix my problem now instead of going through a journey to figure out why it, why it is the way it is and, and how they can actually change their culture a little bit to make, to make the change happen.
Bernita Biekmann (27m 17s):
So yeah, ideally would love to be with, with the organizations that are farther on their journey so that we can use their information. But we've done everything from, you know, we have some that are just, just starting out and maybe their culture doesn't a hundred percent support lean process, process improvement organization wide, but this new department that they're doing, they wanna make sure that they go through the, the project that, of thinking about process before they design and you know, we'll, we'll help them along.
Bernita Biekmann (27m 57s):
We'll do their current state for them, we'll support them, we'll give them the information, we'll coach them through their journey and do our best to create a, create a space that's that's flexible to that journey and can, can support where they're going. And then we've worked with really highly sophisticated organizations that, you know, are already doing their own operational modeling and have full detailed value stream maps before we even start. And that just takes it just to a different level. We can respond to that that differently, but it's kind of full range in between I think most hospital systems these days.
Bernita Biekmann (28m 41s):
I don't, I don't have a fake statistic or real statistic to throw out there. I think the last time I read an article it was like in the 50 to 60% have are at least, you know, saying the words Yeah. At this point. But it's probably way higher than that. I think all of them, most hospital systems that we've worked with recognize that there's opportunities to improve their patient care by looking at process.
Mark Graban (29m 12s):
Right. But yeah, we're probably in, in agreement that knowing the words is a good first step and you
Bernita Biekmann (29m 21s):
Know, yeah,
Mark Graban (29m 21s):
We're, we're, we're both in trying to help move people along in, in that journey, in that process. One, one question, this is more about just technology or the types of things people might ask you about. You know, I, I love the process of doing the mockups, the full scale mockups, the walkthroughs, the simulation of, of the work with cardboard. Do you, do you have anyone push back and say anything like, well that seems really outdated, where, where's the virtual reality technology? And I'm curious if, have you had that thrown at you or, or have you or your firm given any thought to that? Like what, what do you think might happen down the road?
Mark Graban (30m 2s):
Or do you think cardboard is still a pretty effective way, even if that maybe seems old school to people?
Bernita Biekmann (30m 10s):
I, I think that, you know, we, we've certainly used the, that technology before, but there's something about physically touching things and, and phy and physically being in a space and reacting with other humans. Cuz in the virtual reality world, it's the, the thing that, that's difficult. I can show you a perfect space and get you to feel like what it's in that space, but can I get you to feel like what it's like when you have a, you know, a three-year-old crash in that room and you have to work with the other people in that room to, to make, to make sure that you can save that child and make sure everything that you need in order to do that is within close proximity.
Bernita Biekmann (31m 2s):
And the, there's something about that, even if it's just cardboard, that having the physical, the actual equipment there and having three dimensional walls there that I can move that always is more effective or always has been more effective than either the com computer animations or using the virtual equipment. Yeah. Yeah. It's old school, but I don't need any training to teach anyone how to stand in that space and how to react to it.
Mark Graban (31m 34s):
Right. But yeah, I mean it seems like when it comes time to make a change, the beauty of cardboard is that you just physically move it and you don't have to do any computer programming or, you know, it might be slower to do those iterations in a virtual reality environment.
Bernita Biekmann (31m 50s):
Right. And a lot of times you have to have the design a little bit farther along because you have to actually create something for, for that environment to react to. Whereas the cardboard, we can do sketches and build it and have a pretty good representation within a day.
Mark Graban (32m 9s):
Yeah. So how would you, how would you summarize some of the results or maybe, you know, there's certain case studies that, that you would point to, whether you can name names or not, about what the impact has been from going through this lean project delivery approach?
Bernita Biekmann (32m 28s):
I think, I think that the, the, the best impacts are when organizations go through a big cultural change. And I can, you know, Riley Hospital Fertil children for instance, when they went from having multi bay NICU rooms to, to having single, single bed NICU rooms for the nicu, that was a pretty big cultural change. There's a lot of fear there, there was a lot of apprehension from staff. They were worried that they could, they weren't gonna be able to see and, and kind of share responsibilities between staff members. And I think them having the opportunity to get process understanding where they wanted to go, kind of see a future for that actually us physically create that space and walk through it, made that project more successful.
Bernita Biekmann (33m 25s):
There are a lot of changes we did too. If, if you add the complexity of it being an integrated project where we had the people building the project onsite, that there's a lot of small changes we made to increase visibility, decrease costs, so we could spend money elsewhere that led to them having a better space. Akron Children's, we had a lot of the same instances. We had a design for the OR that was everyone loved and kind of sketch form. And when we built it out a cardboard, everybody hated it, you know, based on this well loved progressive model that another large children's institution has got a lot of press over.
Bernita Biekmann (34m 6s):
So, you know, we, we did as close as we could to that. And when they, when they got into the space based on how they operate, how they wanted to operate and kind of the culture, how they work, it was a disaster for them. So in a traditional process, if we would've actually built that based on how happy everyone was with those sketches, we would've been renovating it almost immediately. So there, there are a lot of success, success success stories specifically. I think when people are looking at drastically changing their model and giving them the opportunity to test that, is that really gonna work for you? Does that work for how you, your, your organization is your community is how you wanna practice going forward?
Bernita Biekmann (34m 50s):
And then, you know, there's a lot of cost conversations that we could have about spending money in the right place, spending money on behalf of patient care about taking care of your staff. And we're able to negotiate a lot of that better when we can have those conversations upfront and we can only do that in that kind of environment.
Mark Graban (35m 13s):
Yeah, and there's a lot of great information, you know's, kind of scanning back through the HKS website and some of the case studies. There's a good write up here that you wrote about Akron Children's Hospital. You know, I would encourage listeners go to HKS inc.com or, or do a Google search or HKS lean project delivery and there's, there's a lot of good stuff on the website and there's also a book that, that I've seen that was published by the Akron Children's Hospital people called, I dunno if it's L Cubed or L three, but Lean Operations, lean Design, lean Construction building a Lean Hospital facility.
Mark Graban (35m 55s):
Are there other, one other question I was gonna ask you to wrap up, what, what resources do you recommend because you, you mentioned going, going back and reading the Toyota Way when you were starting with this eight or nine years ago, there probably was not a book on quote unquote lean design or lean project delivery. Maybe there was something on lean construction, but what, what are some of the different resources you would recommend for people to go and learn more today?
Bernita Biekmann (36m 21s):
So there are, I, I think a lot of the, a lot of the resources that we use just for general lean education are good for lean design and construction. LCI Lean Construction Institute has actually published a couple of books most recently a book called Transforming Design and Construction, which has a series of white papers. You can also get to those from their website. If you don't, you can actually buy the book from the website or you can download some of those white papers. There are also this October publishing a book about target value design.
Bernita Biekmann (37m 1s):
And both of these books were written by a collaborative group of, of people that are actually practicing. So, and then they were edited by executive editor or editors depending on the book, but check those out. Those are pretty specific on how liens being applied, design and construction lean, the Construction Institute website is a good resource too for other, other publications and white papers in research studies. So that's a good resource as well.
Mark Graban (37m 37s):
Yeah, and it's, it's totally self-serving on my part to mention, but Bernita you are helpful with, and you're quoted in the third edition of my book Lean Hospitals, where it's, you know, admittedly, you know, small chapter compared to some of these other great books out there that focus more fully and deeply on lean design or, or lead construction. But I would recommend that to people. I, I think I'll, I'll make a PDF of that chapter available on the blog post for this episode where you can see a few comments from Bernita, a little bit of the summary of the Akron Children's Hospital story and, and their results. So thank you Bernita for, you know, helping me out with, with that chapter and for the work that you're doing out there.
Mark Graban (38m 23s):
Sure.
Bernita Biekmann (38m 24s):
Thanks.
Mark Graban (38m 26s):
And you know, with that, I guess we'll, we'll go ahead and wrap up the podcast for today. If people want to reach out, if they've got questions for you, what do you recommend in terms of some ways for people to be able to reach you?
Bernita Biekmann (38m 43s):
They can email me at BBiekmann@HKSinc.com. That's a good way to get ahold of me.
Mark Graban (38m 52s):
And again, as I'd mentioned, there's a lot of great information out there HKSinc.com, the website for HKS Architects. It was really nice talking to you today. Thank you for sharing some of your, your perspectives and helping educate the listeners here about the use of lean and, and building better, more effective hospital buildings and, and clinic buildings. I, I was curious if you have a, a final thought to, to leave with the listeners.
Bernita Biekmann (39m 22s):
Just, you know, encourage the facilities that you work with to, you know, try to improve how they work and, and, and make, make what we do as, as design professionals actually support that work so that we as a group can really make the patient experience better.
Mark Graban (39m 45s):
Well, it's an important goal and, and thanks again for everything you're doing to help people reach those goals. Thanks again, Bernita.
Bernita Biekmann (39m 51s):
Thanks.
Announcer (39m 52s):
Thanks for listening. This has been the Lean Blog podcast. For lean news and commentary updated daily, visit www.leanblog.org. If you have any questions or comments about this podcast, email Mark at leanpodcast@gmail.com.
Please scroll down (or click) to post a comment. Connect with me on LinkedIn.
Let’s build a culture of continuous improvement and psychological safety—together. If you're a leader aiming for lasting change (not just more projects), I help organizations:
- Engage people at all levels in sustainable improvement
- Shift from fear of mistakes to learning from them
- Apply Lean thinking in practical, people-centered ways
Interested in coaching or a keynote talk? Let’s talk.
Join me for a Lean Healthcare Accelerator Trip to Japan! Learn More
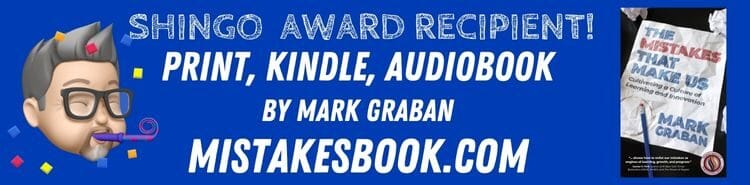