Toyota USA shared a nice video featuring an 11-year old inventor, Bishop Curry, pictured at left with a design drawing. His dad, Bishop Curry Sr. works for Toyota Financial Services and he's also in the video.
The elder Curry works as an “Operational Excellence Consultant” for TFS. From his LinkedIn profile, it sounds like he works to apply the Toyota Production System in Finance (and he now lives near me in the DFW area with the opening of the Toyota North American HQ here in Plano). Welcome to the area!
Hear Mark read this post (subscribe to the podcast)
I've long heard that Toyota hasn't had quite the same culture and TPS / Lean approach outside of manufacturing, but they have been working to catch up. TFS has been a customer of our friends at Gemba Academy as a way to learn Lean (and even Six Sigma, as I've heard, even though Toyota doesn't use formal Six Sigma in their factories). Toyota's not uniformly or perfectly Lean… they're learning and practicing, it seems.
The spread of TPS outside of Toyota factories goes to show that process improvement methods and this management system apply anywhere, as their non-profit TSSC group has long proven in healthcare and non-profits (read more about their 25th anniversary).
It's interesting to see that the word “Lean” is used in his list of methods used in his job profile:
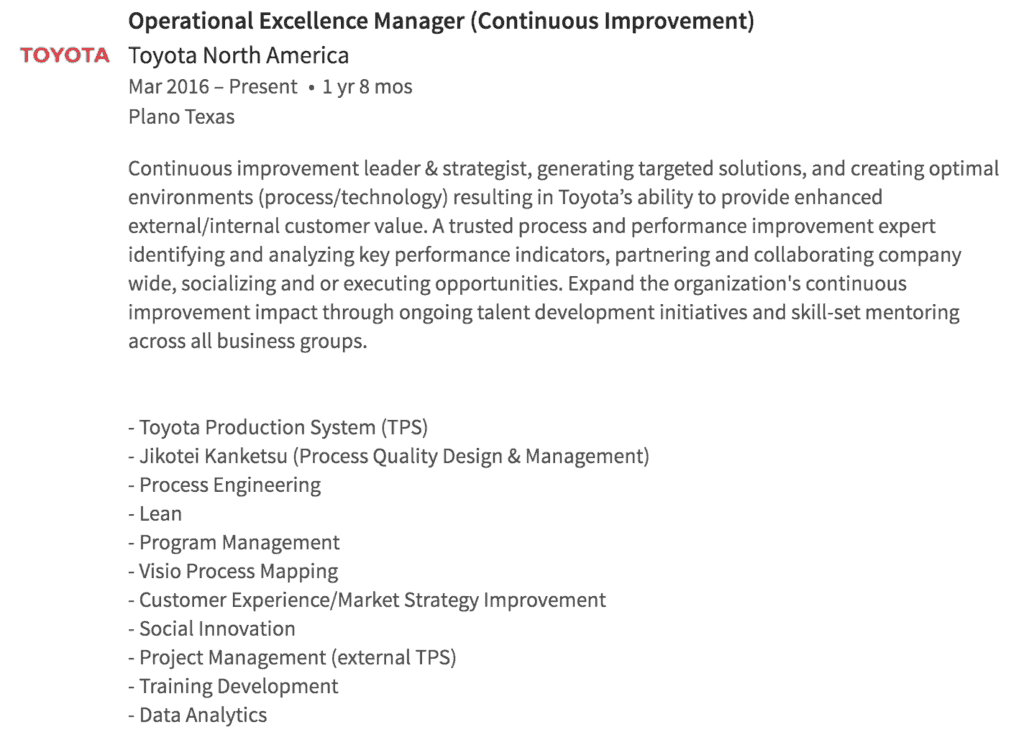
Back to the Young Inventor for a Minute
Anyway, here is the video with 11-year-old Bishop being an experimentalist – thinking like an engineer and an entrepreneur (maybe there's a kid's scholarship available for Lean Startup Week?).
Will his invention work? Is it the best solution? Will anyone buy it or help him produce it?
I don't know. And that's the point… engineering, product design, and entrepreneurship requires experimentation, prototyping, testing, and risk taking. He's learning how to do all of these things. I think that's awesome. He can only prove or disprove his idea in practice, as is true with any startup or big company “intra-preneurship” effort. The same is true with small continuous improvement ideas… we can only prove or disprove that ideas work in practice.
Where I Obsess About Seemingly Minor Details
In the video, some small details beyond his invention jumped out at me. I was looking at his dad's Toyota workplace.
For one, the elder Bishop is shown at his stand up desk (I'm guessing the video was shot back in California, before the move to the new buildings in Texas).
I noticed Toyota is setting a good example when it comes to desk practices (beyond the standing desk and the multiple monitors, which are proven to improve productivity).
When looking at what some other companies do, I've complained for a long time about what I think are misguided “Office 5S” or “Lean Office” initiatives that will insist it's “Lean” to do things like telling employees they must:
- Put tape around your keyboard and desk items
- Remove family photos as “non productive items”
See this post as one classic example of clunky “Lean Office” initiatives that just alienate employees:
Back to Toyota
What do you see on Curry's desk?
FAMILY PHOTOS!
Of course you do. Having family photos there are good for morale. It's humane. There are studies that show it's good for productivity to have family photos on your desk. It also goes to show that Toyota focuses on improvements that matter, rather than mindlessly using Lean tools.
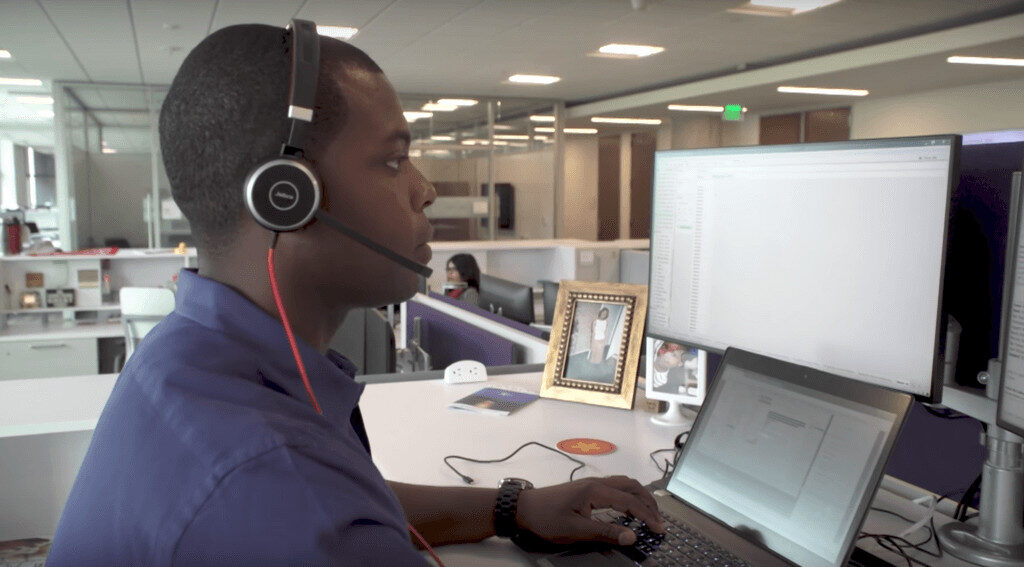
What don't you see?
TAPE AROUND HIS LAPTOP (OR OTHER ITEMS)!
Again, Toyota seems to be setting a good example of not blindly using Lean tools.
By comparison, below is a photo shared with me the other day where a company put tape 5S corners around a huge multifunction copier (not at Toyota, but a large company).
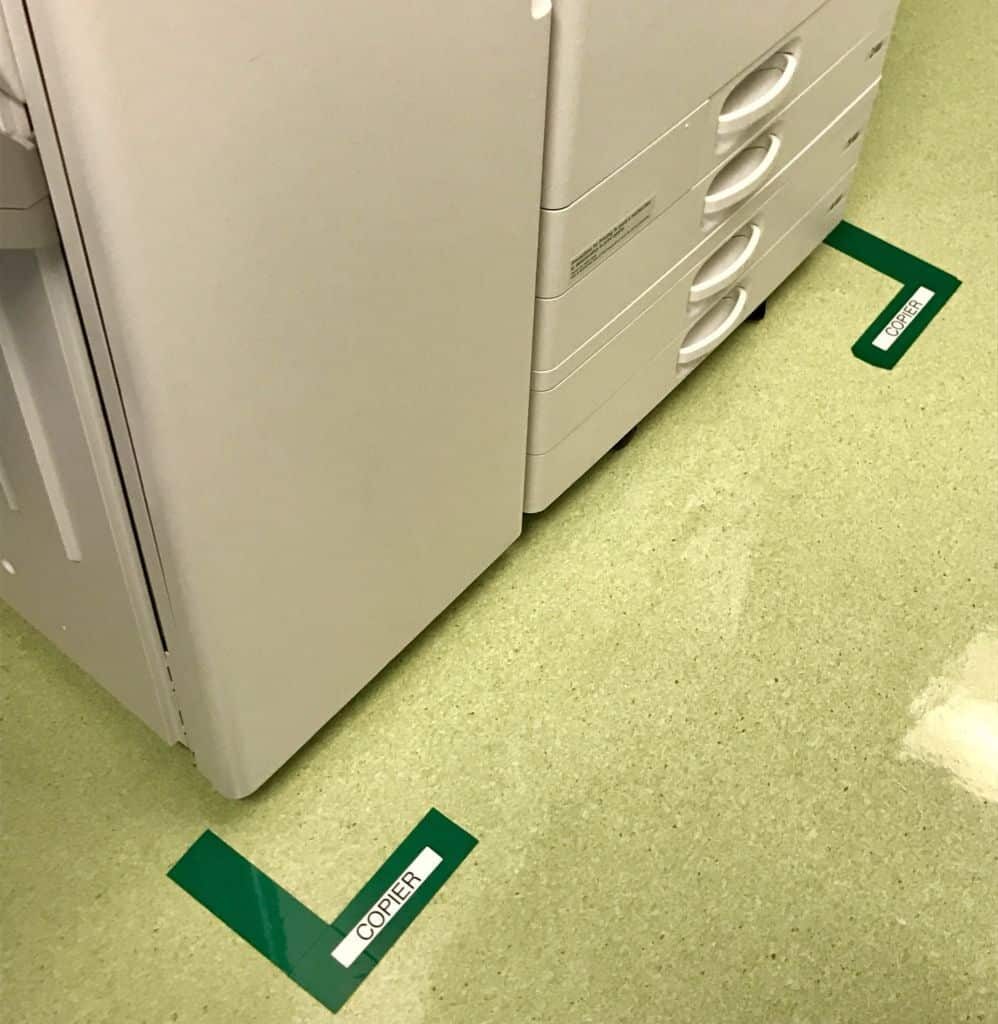
Why did they do that?
What problem is that tape solving?
Has the copier ever moved or gone missing?
Maybe the people who did this didn't have a good coach working with them? Maybe it's an expected mistake that's made as people develop and “practice Lean?” Are the people who put tape around the copier reflecting on what they did and what effect it had?
Are they “implementing 5S” or using a Plan-Do-Study-Adjust process? Are they studying their results, reflecting, and possibly adjusting?
It's Natural to Make Mistakes, But…
I know I seem judgmental when I criticize others for “doing Lean wrong” or using the L.A.M.E. label that I've grown less fond of over time.
It's natural (and expected) that we'll make mistakes or errors in judgment when we're new to anything, Lean included. I made mistakes… and reflecting on that was the inspiration for the book Practicing Lean where 15 others also shared their stories and lessons learned about our early mistakes.
I think all of the contributors to the book were fortunate to have good mentors. They helped us learn from our mistakes.
Hopefully, nobody is making the same mistakes over and over.
One problem with high profile (and, forgive me, misguided) Lean Office initiatives is that it gives Lean a bad name. That might keep others from discovering the true depth and breadth of what Lean is about.
If people hear that Lean is about telling people not to put sweaters on the back of their chairs, they might choose not to learn about Lean and then the might not ever discover the joy of empowering everyone to participate in Kaizen (continuous improvement).
Lean gone wrong leads to articles like this one from TED Ideas:
“Why every office should scrap its clean desk policy”
I agree with the the headline, but disagree with the author's assertion that Lean = clean desk policies.
“… 5S has somehow bled from car assembly lines, operating theaters and semiconductor manufacturing plants, where it might make sense, to the office cubicle, where it does not.”
I agree that clumsy copying of tools for physical spaces might not make sense in a cubicle that's not a shared workspace. My friend Dan Markovitz (listen to my podcast with him) and others have long made the case for the benefits of “information 5S” when it comes to computers and such… those are organizational methods that might actually improve productivity in a way that putting tape around your phone would not.
This TED Ideas article cites a workplace study that I blogged about here:
The one key learning is that morale and productivity improve when employees have some control over the design and decoration of their space. Of course.
The TED article, erroneously equates a “Lean” office with one that's “Spartan.”
“The first was the lean office, a spartan space with a bare desk, swivel chair, pencil and paper.”
A truly “lean office” would be effective – better safety, quality, productivity, morale, etc.
The article draws a conclusion that I'll edit – replacing the word “lean” with the more accurate “spartan.”
“The empowered office was a great success — people got 30 percent more done there than in the [spartan] office, and about 15 percent more than in the enriched office.”
There's a story in the article about Virginia Mason Medical Center that makes me cringe:
“However, 5S enthusiasts at the Virginia Mason Medical Center in Seattle didn't get the memo. Doctors and nurses there were in the habit of hanging a stethoscope on a hook, but management came up with a tidier solution: a drawer marked “stethoscope.” The medical staff kept on hanging the stethoscope on the hook.
What to do? “Eventually,” said a supervisor, “we had to remove the hook.“
It sure sounds like the doctors and nurses preferred the hook. So management removed it? Yikes, that couldn't have been good for morale… and VMMC is often considered to be an exemplar Lean organization with many books out there about their approach.
If you're using a stethoscope a lot, why put it in a drawer if you're going to be accessing it all the time? That sounds like more motion, time, and hassle… and Lean is supposed to REDUCE that. Lean isn't about hiding our tools… it's about having them ready and available to use.
I wonder if VMMC has learned from this? Did the hooks ever come back?
Toyota and Kaizen Recognition
Below is a photo showing young Bishop with one of his engineering mentors.
Behind them is a “kaizen recognition” bulletin board. It's hard to make out the detail, but it's great to see they are giving recognition. That's an important part of the Kaizen process… improvement leads to recognition, which leads to more improvement… a virtuous cycle.
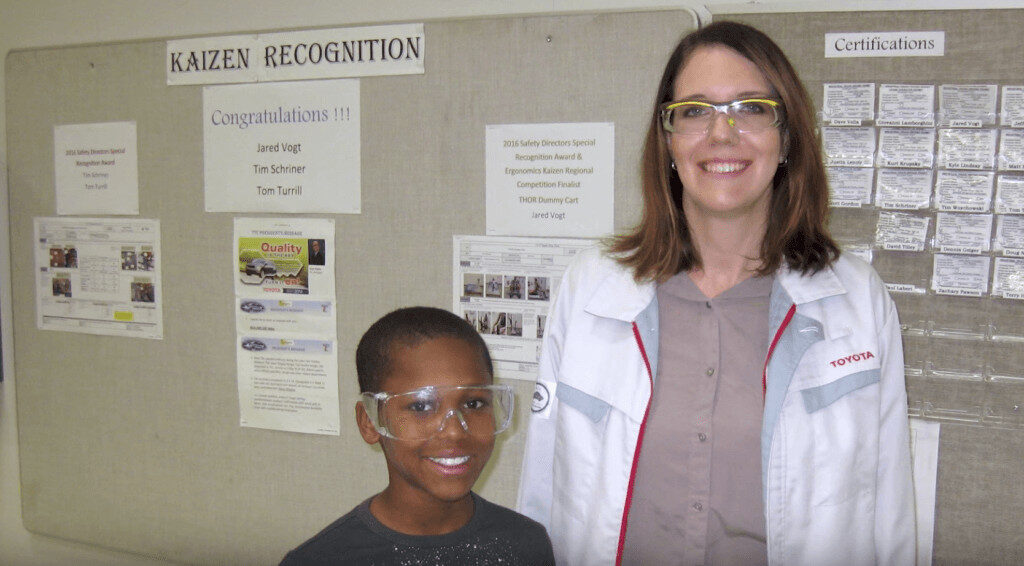
I admire what Bishop is doing to work toward solving and preventing a problem that matters – children dying after being left in hot cars.
And thanks to Toyota for helping him and sharing the story… and the inadvertent Lean lesson.
Here are some of my past blog posts on this topic of “bad office 5S”:
Thanks for reading!
What do you think? Please scroll down (or click) to post a comment. Or please share the post with your thoughts on LinkedIn – and follow me or connect with me there.
Did you like this post? Make sure you don't miss a post or podcast — Subscribe to get notified about posts via email daily or weekly.
Check out my latest book, The Mistakes That Make Us: Cultivating a Culture of Learning and Innovation:
Great post.
I once pushed back on a lean sensei who asked me to use 5S to re-organize my personal workspace (‘what problem will that solve?’, ‘I have my own system’, ‘Nobody else uses the space’). After being worn down by my defiance, he finally explained to me that he was trying to teach me the discipline of establishing a standard, testing a standard, and improving a standard – NOT how to improve my organization skills or even remove waste. Through this lens, I more readily understood the purpose of the lesson (I still didn’t agree with it and we used a different routine to practice on).
Frighteningly, 5S is a common entry-level lesson used to introduce people to Lean, often taught from a starting set of principles of “eliminate variation through blanket standards” and “inspect for compliance” – principles I’ve come to know as antithetical to lean thinking principles. This approach is often positioned as the “foundation of Lean”. If this is the foundation, it’s no wonder that staff and leaders hate it and don’t sign on for more. Start from (useful) principles and start from need.
Thanks for sharing the story, Ryan.
I agree that there are probably more meaningful places to learn and practice 5S… such as a real business problem that would make somebody’s work easier. Then we’re demonstrating that 5S and Lean are helpful instead of then forcing people to “buy in” or go along with what we’re telling them to do… even if it’s for their own good.
Your sensei was well intended… but I think we need to have a better recognition that “do this because I said so” (even when it’s “good for” the person we’re pointing that) isn’t a good pathway to change. We might get, at best, compliance… and that’s not what Lean is about.
I wish folks would think and use judgment instead of falling back on “we should always start with 5S.” Why? “Because that’s how I was taught.”
5S can be a VERY helpful method and a great way to get started… except when it’s not the right way to start.
[…] Sourced through LeanBlog […]
Read Michel Baudin’s thoughts here…
He starts:
Click the link above for his full comments…