Back in September 2015, I wrote a post (“Learning to be Lean” – An Inside Look at a Rapid Improvement Event“) that linked to a Modern Healthcare article about a Rapid Improvement Event at Presence Health in Illinois.
The piece was written by journalist Sabriya Rice, who had been allowed to participate in the event. The event was claimed to have reduced operating room turnaround time, which “has the potential to add $600,000 of added revenue over the course of a year.”
Of course, “potential revenue” is not the same as “actual revenue,” but, still, it sounded like a reasonably well run RIE that showed promise. But, we didn't know if Presence was just running some random projects or if they were on more of a ThedaCare path. ThedaCare, of course, started out primarily using RIEs to engage people in the first few years of their Lean approach before waking up to the fact that they also needed to change the management system and engage everybody in daily continuous improvement.
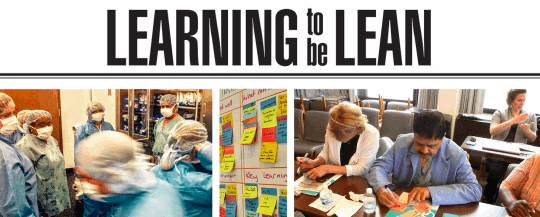
ThedaCare has been on their “Lean journey” for about 14 years now. The program has become, pretty much, “the way they do things” and it survived the transition from one CEO (Dr. John Toussaint) to another (Dr. Dean Gruner). Gruner was promoted internally from CMO because the ThedaCare board wanted Lean to continue.
Apparently, the Lean journey at Presence, regardless of what form it was taking in late 2015, has not survived a CEO transition at Presence Health. A new CEO, Michael Englehart, took over about six months ago (just after that Modern Healthcare story was published).
Hear Mark read this post — subscribe to Lean Blog Audio
Here is the latest Modern Healthcare piece by Sabriya Rice:
“Presence Health rethinks its Lean initiative“
“Rethinks” is an understated headline, given what seems to have happened.
“Former CEO Sandra Bruce brought the concept in 2012. Bruce retired last fall.
A Presence Health spokesperson said in an e-mail that it “is in an ongoing process to position all system hospitals for long-term growth and viability.” Upon evaluation of the Lean program, “we saw ways to enhance it and align it in a more focused way to serve our patient and business needs.”
I have no idea what the corporate speak of the second paragraph means.
Evaluate? Enhance…. align it?
An unnamed source was more blunt:
“Sources close to the situation tell Modern Healthcare that new leadership was “not a fan of Lean” and that the program has been disbanded.”
I had one Presence Health employee connect with me on LinkedIn and, when I asked them about what happened with Lean, they wrote:
“Yes, the rumor is true the Breakthrough Improvement department at Presence was disassembled as of 4/15.”
This person had already accepted a new Lean role at a different health system, so they probably saw the writing on the wall.
Again, from Modern Healthcare:
“A Presence Health spokesperson did not say whether the system's new direction would still include those weeklong breakthrough events.”
It sounds like they won't be.
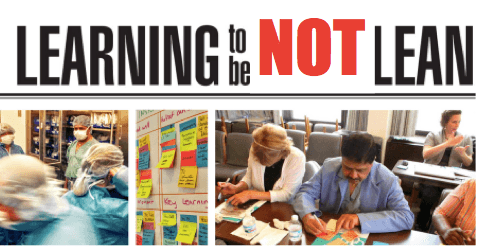
Why Would a CEO Not “Be a Fan” of Lean?
Sabriya Rice called me on Thursday to get my perspective, as she had quoted me in her article from September.
We had a relatively long chat where all I could do was speculate about why these sorts of things happen. Let's try to brainstorm them here (and post a comment, below, if you like).
I haven't needed Lean before. This is one I've heard back in 2011 when I was writing the second edition of Lean Hospitals. One hospital had been featured pretty prominently in the first edition — they were doing Lean projects, using Lean design to build a new Emergency Department with better patient flow (pretty innovative for ten years ago) and their main Lean champion was a VP who was trying to influence culture change. In my research for the second edition, we quickly all agreed to not include that hospital in the book anymore. I was told, second hand, that the new CEO had been successful at their previous stops (they were an outside hire) and that Lean wasn't needed there. The Lean champions and change agents basically all left and went to other health systems.
That's sort of what I was thinking of when I was quoted in the new piece as being opposed to arrogance:
Leadership arrogance, [Graban] said, is often another factor.
“People think that through the force of their personality or financial wizardry that they are going to be able to fix a hospital without engaging employees in the improvement,” he said.
I knew I was being provocative. Not all healthcare leaders are arrogant, of course… but there are too many who are. Compare that to the humility that's a key aspect of Toyota or a Lean culture.
I don't understand Lean. It could be that a new CEO comes in and is pretty ignorant about Lean. They don't have any experience with it. Maybe they've somehow gotten the idea that Lean is all about cost cutting and they're already good at cost cutting (which probably means layoffs, which is NOT the Lean approach).
Ten years ago, when I started, it was a challenge that healthcare leaders hadn't even heard of Lean or the Toyota Production System. Now, they've heard of it, but many haven't taken the time to really learn what it is.
Lean wasn't making a difference. It could be that a hospital wasn't really getting good results or sustainable results with their Lean approach. Maybe the retired CEO had paper-thin support for Lean and basically just approved some spending on projects or a consultant. Maybe the RIEs weren't really engaging people. It could be they were just running some random projects in the same, old, broken healthcare culture. A Lean approach is supposed to simultaneously improve quality and reduce cost (again, cost reduction isn't the primary goal). If Lean wasn't accomplishing any of that… should they have been more patient or should they have ended this attempt?
Either way, it's sad to see a hospital give up on Lean… or to have killed an initiative before it really could have made a difference?
What do you think? There's been some good discussion about this on Twitter:
What do you think, either from your own experience with the demise of a Lean program? Or would you recklessly brainstorm and speculate with me?
What do you think? Please scroll down (or click) to post a comment. Or please share the post with your thoughts on LinkedIn – and follow me or connect with me there.
Did you like this post? Make sure you don't miss a post or podcast — Subscribe to get notified about posts via email daily or weekly.
Check out my latest book, The Mistakes That Make Us: Cultivating a Culture of Learning and Innovation:
[…] Update: See this April 2016 post about the health system apparently killing its Lean program […]
I’ve experienced another trait of some of these “New CEOs.” One of the pillars of Lean – Respect for People. This is tough – giving someone else the power to change things in the organization. When a new CEO comes into an organization, especially if they have not been part of the unique Lean culture within that organization, they feel the need to justify their position/salary. I can imagine, to an outsider, that a robust lean culture is intimidating …. line employees making decisions about how activities and processes happen that influence quality, productivity, profitability. I can imagine the unspoken thought, “I’m the head-honcho around here – I’ve got more education – I’ve got more experience – shouldn’t I be the one making the important decisions?” I wonder if this new CEO would be willing to work side-by-side an intern in the stockroom to reorganize the bedpan inventory (how humiliating!)
Maybe this is just as much a lesson for large organizations doing succession planning …. if you already have a healthy lean culture, groom someone from within that culture to take on the next leadership role. Perhaps this is just as much a failure of the previous CEO to neglect succession planning as it is the new CEO for being ignorant about the system benefits of lean.
It’s possible they didn’t have “a healthy Lean culture.” It’s possible they just had a bunch of events and projects. It’s possible that the now-retired CEO wasn’t driving culture change. We don’t know.
I had the opportunity to serve as an “outside set of eyes” on one of Presence’s rapid improvement events in March. It was well facilitated and the assembled team were committed. Clearly the Breakthrough Improvement program was accepted and integrated on floors and staff because when we went to run tests and eventually do education on the improvements, staff readily supported the work. They saw the value in improvements made by their colleagues. It is a shame to do away with such skilled facilitators and wipe out the progress they made in their Lean journey.
Mark, in our experience, CEO transition (outside hires) are the #1 failure mode of a Lean initiative.
However, done correctly, a Lean Enterprise Transformation including development of the Business management system, results in promotion from within and a culture pf continuous improvement and respect for people that thrives in transition rather than simply surviving.
John
My experience has been the same as John G’s. New CEOs come in with a list of their own priorities and if it doesn’t include Lean, then Lean becomes something that takes focus away from what they want to do.
I found the Thedacare example insightful: “the board wanted Lean to continue.” That seems like such a key piece, given that the average tenure of a CEO is probably less than the time needed to establish a Lean culture strong enough to survive a turnover.
No surprise. Changes in ownership and changes in leadership are the biggest killers of progressive management in organizations. The former is highly probable while the latter is almost certain.
I wrote the second edition of Better Thinking, Better results to highlight this failure mode and suggest ways to avoid it.
Apparently the former CEO did not plan to avoid such an outcome.
Also see the discussion on LinkedIn, including:
I’ve been a Lean consultant for about 17 years. I do not know how to sell Lean to a CEO. Such as Mr. CEO, or owner, I realize you have made millions of dollars, supported many families through your business for many years, but you have really missed out by not applying the elements of Lean in your organization. You could have made much more money and made work easier and better for your employees.
Every one of my clients were looking for change, improvements, Lean when they found me. They needed better results from their efforts. I have a few horror stories about Lean being derailed, but most of my efforts have been successful.
So, why do some CEO’s kill a Lean program? Because we simply haven’t discovered how to sell Lean to someone who is ignorant of what Lean really is. CEO’s are smart, or they wouldn’t be in that position. They are just ignorant of what Lean is and why nothing about Lean is negative for an organization or it’s employees.
When it comes to preventing failed businesses, low profits, bad quality, etc. we must learn how to convince CEO’s what Lean amounts to and why they need it.
From the standpoint of a current Presence Health Employee~ my opinion is that the RIEs failed because they were aggressively site specific. At a time when Presence Health is “Becoming One” I do not believe the RIEs took the entire ministry into consideration when planning events. Decisions and “experiments” where being made and conducted through a site specific lens, and this was often in contradiction to the spirit of the new organization.
Thanks for your comment. I can understand the need for common processes (or every site in an organization improving).
I still don’t understand the desire for “Becoming One” running counter to Lean. I don’t understand that as a reason to kill Lean.
I can only hope the reporting is wrong or that the health system just hasn’t explained well how they are taking a new direction with Lean. The status quo in healthcare is so bad… so much improvement is needed. I hope Presence Heath can accomplish whatever needs to be done in whatever way they choose.
But Lean should be a big contributor to all of those goals…
[…] you read that post, there’s an interesting comment from a Presence Health employee that doesn’t shed too much more light on […]
From LinkedIn:
Richard Crespo, J.D., PMP, SMC:
“Mark Graban unfortunately there are many in healthcare who do not appreciate the value of Lean in a healthcare setting. Root Cause: Arrogance and unwilling to explore and benchmark from industries other than healthcare. In addition, healthcare seems to lag in technology especially in the administrative areas where waste accounts for a lot of the lack of productivity. Still, there are some in healthcare who understand the value of Lean but they are the minority. Good article!”
Another reason is hiring the wrong CEO. Many corporations promote the wrong people-dynamic abusers instead of servant leaders, and if leadership doesn’t understand the difference, they look the same.
See the book ‘Snakes in Suits‘- truly chilling.
The biggest problem with Lean projects has been the ability to get buy in from top level execs who can be game changers in the success in a Lean campaign.
CEOs, CFO, Executive VP’s, in my experience really don’t find value in the Lean process clearly because subordinate level execs are afraid to push forward the value in Lean and are often spending time trying to impress with traditional cost saving rhetoric at executive level meetings.
Successful lean execution begins with an executive plan to commit to the process and making it part of the corporate culture, set the example by following through with the process, and making sure the process is systematically filtered down to the lowest paid employee. If managers and supervisors aren’t given a mandate from their directors, VPs. and chief executive offers, how effective can it really be?
Individual departments can challenge their interdepartmental processes to improve by using lean unfortunately they run in to toll gates at the end because they will need to interact with other departments that have not adopted the Lean culture, therefore creating a viscous cycle of frustration and skepticism in the Lean system.
In the past we have seen this happen when it was called TQM (Total Quality Management), Six Sigma, along with a host of other names. At the end the success is based on corporate wide acceptance to making change for the better, rolling up the sleeves, refreshing to make a new start and committing to a better way of thinking.
I think a CEO that is not a fan of Lean simply doesn’t understand how — introduced properly — it transforms the workers. I’ve been asked by a COO, “How does Lean make a difference? We are doing all those things anyway.” I respond that, yes, the company is already working on fixing broken processes, lowering cost, and increasing productivity; however, Lean maximizes those results, helps them come about faster, and encourages the workers to keep finding ways to improve. During a Lean simulation in a class I teach, we have a team work together to streamline a process that originally takes 8 minutes to perform. A traditional improvement approach may take that process down to 6 or 7 minutes. After learning Lean tools and concepts, the team takes the process down to 2 minutes. They also realize that their leaders wouldn’t have been able to create that new and better process. It took working within that process and collaborating with the other team members to know how to maximize the improvements. An additional benefit was that the workers were empowered by the experience and wanted to keep looking for ways to improve the process. You don’t get that from a traditional CEO sending out a crack team of managers or consultants to impose “change” on an organization.
When hearing
That’s often wishful thinking on the part of executives.
“Lean, we already do that, but we just don’t call it Lean” is usually not true.
[…] Why Would a New Healthcare CEO Kill a Lean Program? […]
[…] ARE organizations that have given up on Lean. I wrote about one earlier this year, related to a hospital that had a new CEO kill their Lean program for unknown […]
I’m really surprised by our willingness to ascribe the failure to sustain a Lean program to the short-sightedness of “arrogant” executives rather than objectively examine other potential root causes. Most of the replies here could be summarized by “things would be so much better if only executives were as smart as us Lean folks”. There are other reasons for killing a program;
* “Project savings” exist on paper only. If you’re claiming $500k savings, yet I’m not seeing it on a P&L? It doesn’t exist.
* Working “successful” projects that aren’t aligned with defined organizational strategy. Or sub-optimizing processes at the expense of the broader value stream.
* Hitting your target on only a small percentage of projects. That $500k you saved may not make up for the labor hours spent on 20 other projects that failed to realize any benefit.
* Training lots of people yet not re-engaging their new skills on continuous improvement initiatives.
These are only a few reasons that a new CEO might kill Lean that otherwise appears successful. I’ve seen more bad Lean programs survive executive turnover than I’ve seen good Lean programs killed.
Robert –
Thanks for your comment. Those bullet points of yours are good descriptors of a “bad Lean program.”
The one bullet point, though, sounds like the type of Lean program that’s only concerned about ROI/cost savings, which is a different type of bad (if they’re ignoring safety, waiting times, etc. that don’t have direct ROI, but rather indirect benefits that are harder sometimes to connect to a specific project or improvement).
Many of those bad Lean programs get into that state because they’re not strategic corporate initiatives owned by the senior leadership team. What you describe sounds a lot like a delegated “Lean Tools” program or “Lean Projects” (or “Lean Training”) as opposed to a full “Lean Transformation” approach that includes culture and management system… things like ThedaCare and some other leading organizations would do.
There are situations, including here, where it’s been reported to me that the new CEO said basically, “I was successful without Lean in my old organization, so it’s not needed here.”
That could be described as being arrogant… or maybe ignorant, or closed-minded or set in their ways.
Either way, it seems like the Lean program described here was driving results and had real potential. The same was true in this other case example.
I think it’s sad.
I think it’s important to think and talk about why this happens and how to prevent/avoid it… it’s not always because it’s a “bad program” there.
Only a small fraction of “Lean” programs (or “Six Sigma” programs, or “TPS” programs for that matter) are true full transformational systems. Those are rare exceptions. Most are training-based improvement programs, departmental/tactical improvement programs, or some other narrow segment of the elements required for a truly transformational system. Most programs are tenuous at best. Ask a deployment leader what percentage of his/her green belts complete another project after certification. Ask a kaizen leader how their project’s objective maps to an organizational strategic objective. Ask a deployment leader what would happen to the improvement initiative if their role went away. Most deployment leaders would be uncomfortable with the answers to these questions. And that makes their programs susceptible to the whims of leadership.
This isn’t new and it isn’t specific to Lean. Russ Ackoff identified this fifty years ago when he noted that 2/3rds of quality/improvement initiatives fail. Sometimes that failure is directedby the hands of a new CEO and sometimes its at the hands of the current CEO that isn’t happy with the return on his organizational investment.
As Lean/improvement leaders, CEOs are our customers (whether we like it or not). If any other customer stopped buying our product, I doubt we would shrug off any blame and instead brand them as arrogant or close-minded. We would instead try to figure out what it was about our product that made it undesirable. Cost, quality, features, packaging, etc. The unwillingness to hold ourselves personally accountable for the failings of our program is the antithesis of where we should be. I’ve led and been part of programs that didn’t reach the levels I thought they should. But that didn’t happen because some executive was short-sighted. It happened because I didn’t do the work required to make the program indispensable to organizational strategy.
Good points.
To your last paragraph though, Lean isn’t the same as a consumer product, like a box of soap that’s simply being “sold.” Lean requires a change in thinking that many executives either think isn’t necessary for them or it’s just of no interest.
I’d question the problem solving ability of a CEO who comes in and immediately kills a Lean program, especially one that seemed (from the outside) to be delivering meaningful results. Labels like “arrogant” are only speculation and probably not helpful, you’re right.
I’m just an outside commentator here. When I’ve been a part of Lean initiatives that weren’t grabbing the attention of leaders or staff, I challenged myself to understand why and to work with people, not blame them. But, I’m not on the inside of that situation.
You raise good points about how people should look at and think about the Lean efforts they are leading or are a part of.
Thanks for the comments and for challenging my thinking and writing.