Is it Really Lean if the Employees are Upset? Understanding the Importance of Employee Engagement…
How is it that we have two realities out there in healthcare… in parallel, Lean is awesome and Lean is horrible. It depends on where you are, unfortunately.
I had an amazing day yesterday at Cleveland Clinic… and I'll blog more about them later (Update: I did). I was their guest to see their progress with Lean and continuous improvement (Kaizen).
I saw staff members enthusiastically explaining their continuous improvement approach. Nurses in multiple departments, environmental services, patient transporters. They're doing A3s and structured problem solving. They're identifying problems and implementing staff ideas in visual ways.
Staff members are telling management what problems they want or need to fix and they're being given time to work on things, with the support of coaches. These coaches are their managers and continuous improvement professionals.
The staff members demonstrated a high level of mastery of not just the tools and methodology, but the mindsets, saying things like:
- We're pointing fingers less and looking at the process
- We're testing countermeasures to see if they work
- We're looking for root causes instead of being happy with workarounds
- We might not totally solve the problem, but we'll make it better and come back to try another improvement
- We thought we were good until we started studying the process and then we saw how much opportunity we have
They are getting results – shorter patient waiting times, faster call light response, higher patient satisfaction, lower cost… and they're working to demonstrate and measure the impact on quality and safety.
I think any Lean skeptic would be blown away by the smiles, the enthusiasm, the empowerment, and the patient-centered-ness of this.
Hear Mark read this post (and subscribe to the podcast):
So, it was heartbreaking to once again read about the complaints about Lean in the Saskatchewan healthcare system (read previous posts about their problems and controversy).
It's so confusing, trying to figure out this Saskatchewan situation from afar.
I saw this headline:
Impossible to say if Lean program working: Provincial auditor
I haven't read the whole report yet, but the CBC article says:
“While some aspects of the government's multimillion-dollar Lean efficiency program are effective, the provincial auditor says she's still not getting an answer to her big question — does it work?”
For one, I hope calling Lean an “efficiency program” is the media's mistake. Lean is about improving flow and quality (just ask Toyota)… better efficiency and lower cost would be end results of meeting those goals.
“Ferguson said there's evidence that the program is being effectively co-ordinated — but not whether it's leading to better service, improving things, or getting good value for the money spent.
“They're unable to show us whether or not Lean is achieving what they're hoping it's achieving,” Ferguson told reporters.
The auditor had come to similar conclusions in a previous report that looked at Lean in health care.”
Internet reader comments sometimes have to be taken with a grain of salt… and this Saskatchewan situation has become a partisan political fight, but look at the comments:
lol…and you wonder why there are high sick days?
lean=stressed out employees, cuts and overworked staff. period
And
Doc here. Can confirm, LEAN is a ridiculous joke. I do not know a single staff member of any level who I have asked, who thinks it doing anything, but it has universally wasted our time and made working more difficult.
And
Does Lean work? Just ask any front line health care worker affected by it, they're the ones that have to put up with it day in and day out. All those this poster knows of all say it's a complete wa$te that's made their all ready difficult jobs (due to the epidemic of under staffing) even more difficult.
And
Most staff were never consulted before the gov't brought in this private consultant, and if they had it would have been pointed out that many lean-type initiatives that help the workplace run more efficiently were already in place, developed organically through common sense as well as prior continuous improvement initiatives undertaken by management. The consultant never came and said “oh i see you are already doing such and such parts that are already fit into lean”, rather he just said “this is how you do it” and our gov't and healthcare administrators forced it into hospitals with no regard for the daily effort that staff have already been putting in to making sure their jobs went as smooth as possible.
And
LEAN is just like the ShamWow, big on hype short on results. Obviously the government needs to hire more Vince-like ShamWow communications staff to hype it up. The alternative would be to show these LEAN leach consultants the door and hire some competent managers.
And
LEAN is the only program I have heard of that spends $100 MILLION to save $30 million.
John Black and Associates sure proved that there is a sucker born every minute and that Brad is one of them.
So, how can be it that the hospital I visited yesterday is using Lean (engaging staff) to make work EASIER, while people in Saskatchewan (and some other hospitals, unfortunately) claim that Lean has increased stress and is making work more difficult?
Why are there so many complaints?
Saskatchewan has taken the wrong approach to Lean? It's too top down? They tried to do too much too fast? Didn't engage the staff like I saw yesterday?
Does Saskatchewan have a communication problem? They are doing good things, but not communicating it internally or externally?
When Lean is done well, properly, you don't hear those complaints.
Recently, I heard an American Toyota executive say, “If the employees are upset, it's not really Lean.”
An American Toyota executive said: If the employees are upset, it's not really Lean. Share on XWhat do you think?
Please scroll down (or click) to post a comment. Connect with me on LinkedIn.
Let’s work together to build a culture of continuous improvement and psychological safety. If you're a leader looking to create lasting change—not just projects—I help organizations:
- Engage people at all levels in sustainable improvement
- Shift from fear of mistakes to learning from them
- Apply Lean thinking in practical, people-centered ways
Interested in coaching or a keynote talk? Let’s start a conversation.
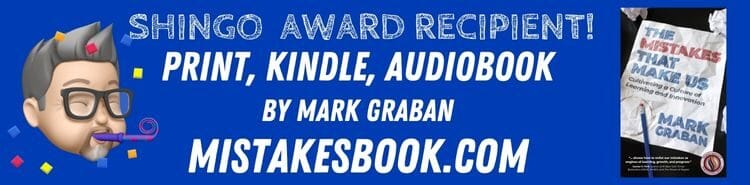
Interesting point on Twitter:
Yes, Lean and improvement can push people out of their comfort zone. But they shouldn’t be completely upset and disengaged, either.
Totally agree with you Mark.
And it’s often the same root cause : only “tools” deployment…
Instead of this ToolsOfFakeLeanMania, they can choose the right way : Develop people.
Sab
It’s unrealistic to expect that every Lean implementation is going to be equally effective or that every consulting group is equally competent. Add to that that healthcare is different from where many consultants earned their stripes. There’s also a wide spectrum of entry points for healthcare organizations. As pointed out by you and Sab, ultimately it comes down to the effectiveness of the leader. More recently, much has been written on this topic but still not widely understood on how to be an effective Lean leader. It is also unrealistic to expect every healthcare leader can be an effective Lean leader.
What puzzles me about Saskatchewan is that they appear to have some success stories with Lean:
Yet some say Lean is not working there or that Lean is upsetting and alienating people…
And this sounds positive:
I think that when people who have been doing a process for so long and are told that they are doing it wrong and that it could be done more efficiently this way, they will automatically look at the new process with a negative attitude . And if you’re feeling negative, you will only look for the negatives, and all you will find is negative problems. when you talk about lean I think everyone should be involved and be able to put in there input as to why something will or won’t work. and I completely agree with the quote “If the employees are upset, it’s not really Lean.”
Wow, interesting post! When executed correctly, lean makes everybody’s life easier. For lean to work, EVERYONE has to be on board and actively involved in creating an environment that strives for better quality and improved flow.