tl;dr: In this post, Mark examines the concepts of “Flow,” “Push,” and “Pull” within the context of hospital operations. Drawing from Lean principles, he delves into the advantages and disadvantages of each approach in managing patient care and resources. Mark argues that understanding these operational modes can help healthcare organizations optimize efficiency, improve patient outcomes, and reduce waste. The post serves as an insightful guide for healthcare professionals interested in leveraging Lean methodologies to enhance operational effectiveness.
Of all of the different Lean concepts, it seems that the question of “push” versus “pull” is often the most confusing for folks in healthcare. I tried to address this in my book Lean Hospitals, but I see a lot being said or written about “pull” that doesn't quite capture the concept.
This is not a question of whether we physically push or pull a patient's bed as they're rolling down a hallway. That's a matter of ergonomics. What I'm talking about is the conceptual “pull” of resources (rooms, medications, doctors) when needed by the patient.

People sometimes say,
“We already have pull. We pull the patient to the room when it's available.”
No. That's not pull. Pull is making resources, again, when needed by the patient. Not when the resource is ready.
Before we get to the healthcare topics, please bear with me for a little bit of manufacturing context on the words push and pull.
What is “Push” in Manufacturing?
Before we can understand “pull,” we have to first understand the traditional way in manufacturing — what we call “push.”
In a “push” environment, we're generally producing goods without real regard for actual customer demand. If you're from healthcare, this might seem silly. Why would you build products that aren't needed by customers? Why would you order supplies that aren't needed for production?
Push production is often driven by a production schedule that's created in advance, based on a forecast of actual demand. Forecasts are usually inaccurate, even with fancy computer systems. A factory or a department might have a computerized schedule that says to build 500 of something daily. The factory managers, in their silo, are often judged based on their ability to meet the schedule. So, they try to build 500 a day, even if inventories of finished products are accumulating. That manager's job is to build them… it's somebody else's job to sell them.
One of the problems with push is that inventory accumulates — either as “finished goods inventory” or “work in progress” between steps in a value stream.
Why would a factory keep building stuff if they are building more than customers demand?
One reason is that managers are afraid that machines will break down. So, if the machines are running smoothly… keep 'em running. Keep 'em cranking out parts. We'll build up inventory just in case the danged thing breaks down tomorrow. We'll use the inventory or sell the products eventually.
Another reason a factory will keep making products is to spread out its overhead costs. In some cost accounting systems, making more parts means each part is cheaper because the overhead is spread out across, say, 600 units instead of 500 units. The cost might seem lower in that one silo, but now the company has the cost of storing and moving that inventory, along with the other risks that come from holding inventory.
Examples of “push production”:
- A fast food restaurant making food and storing it under heat lamps (some of it gets thrown away)
- An automaker building an excess number of cars or trucks and forcing the dealers to take them
- The U.S. Mint producing dollar coins that far exceed customer demand
- Computer makers building product and shipping it to retailers to sit on the shelves
- Starbucks brewing batches of coffee based on a forecast
- A hospital pharmacy making IV bags based on expected usage
It's hard to find examples of “push” production in healthcare. The hospital cafeteria might do “push” production of food items (made in advance based on a forecast). Same might be true in the pharmacy. So much of what we do in healthcare is done “on demand,” that it is essentially “pull.”
Sometimes, “push” works out OK. We might have very known and steady demand. The amount pushed might happen to be the same as what's consumed by the customer. But, push often causes many problems.
What is “Pull” in Manufacturing, and How Does It Help?
“Pull” is the concept of basically building in response to actual customer demand OR restocking inventories in a controlled way based on the customer's consumption of products. Pull reduces costs, improves quality, and makes sure the customer gets what they want, when they need it, in the right quantities.
Some examples of pull (or push combined with pull), based on the bullet points above
- Chipotle makes a specific burrito when pulled by the customer (but the meat and veggie components might be cooked based on push, potentially)
- Starbucks makes a specific latte or beverage based on a customer order or pull signal, but the milk might be “pushed” to the store based on forecasts
- In many stores, Starbucks can brew a single cup of coffee for you based on a pull signal, in a french press or a Clover machine.
- You special order a specific car or truck from a dealer and it's built specifically for you (possible, but it might take weeks or months, even from Toyota)… many of the “pull signals” in the auto industry are from the dealer, who is predicting what you'll want to buy
- Dell Computer, back in the day, did “build to order,” building and ordering after you ordered it on the web (but components were purchased from China based on forecasts)
Even in those examples, “pure pull” (where everything is done only in response to a customer order) is hard to find. It's easier to do “pure pull” when the production times are short and the supplier is close to the customer.
For example, let's say I wanted to buy a Toyota pickup truck that's made here in San Antonio:
- My pull signal (singing a contract with Toyota) would lead to them starting final assembly
- Final assembly would pull all of the components (stamped metal panels, plastic pieces, electronics, tires) directly from a supplier
- Some of those parts are assembled by on-site suppliers (such as dashboards and seats)
- The dashboard and seats have purchased components that might come from some distance away…
So when there's some time and distance involved, Toyota will choose to have an inventory of parts. It's not longer “pure pull.” Toyota sets inventory levels based on the expected usage of parts (so a forecast or prediction is involved somewhat).
But, the supplier is not authorized to keep shipping parts because the forecast said so. Toyota has inventory limits and a “kanban system,” where you use some and you order some. So, the replenishment of parts is driven by actual usage… if none are used, none get replaced. That's a form of pull, as well.
Here's a video from my friends at Gemba Academy on Kanban systems:
Pull systems are helpful because they set limits on inventory levels. There's a discipline that says either:
- We have no customer demand, so we don't build or
- Inventory levels have hit their max, so we stop building
Again, in a push system, people are tempted to EXCEED inventory levels because they think that reduces cost to keep building. A Lean thinker realizes it's more costly, generally speaking, to overproduce. During the 2008-2009 financial crisis, Toyota stopped production for three months because inventory levels had gotten too high (and they didn't layoff full-time workers, but that's a different story).
Here is a video by Jay Arthur about Pull and Push:
From a Toyota instructional booklet:
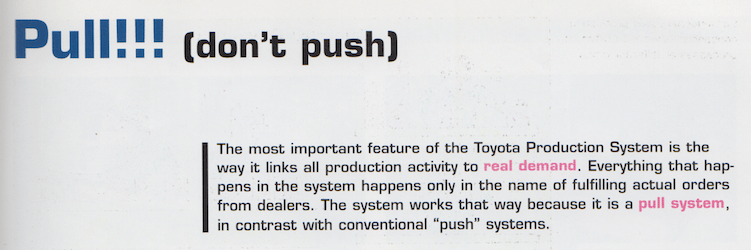
See, it's about “real demand.” What's the “real demand” in our hospital? Hint, if patients are waiting, real demand isn't being met. Notice also how Toyota admits they are building to dealer orders, not the end car-driving customer… but it's better than pushing cars to dealers based on our own forecasts or schedules.
The Goal is Flow – Right Care, Right Place, Right Time
Whether we have push or pull, or a combination of the two, the real goal in Lean is FLOW – matching production to consumption, matching supply to demand.
As Jim Womack, Jeff Liker, and others have taught:
Flow where you can, Pull where you must
Rather than quibbling over “push vs. pull,” the real challenge for healthcare is figuring out how to improve flow by reducing waste in the system.
What Does This Mean for Healthcare?
It means we need to think about “pull” as the patient pulling resources that are needed. Doing work when patients need the care, rather than doing it when it's convenient or when we happen to have the capacity.
Not what we mean by “push” vs. “pull” – one person is pulling the bed and two are pushing it… it's not the physical movement of the patient, but the match of patient needs to the care provided.
If we move a patient from the ED to an inpatient bed because that bed was made available when the patient needed it (at a physician's admission order), then that's pull. That gets confusing, because we are moving the patient, but the patient is pulling the bed/room.
What's sometimes called “pull until full” in the E.D. is sort of pull… if a patient comes to triage and registration and they need a room, the patient is requesting a room and they get a room. The patient has “pulled” an exam room. But, if there's no doctor or nurse available, we have just moved the wait from the waiting room to the exam room… that's poor flow.
Let's say a patient needs blood work done. An order is put in and a nurse (or a phlebotomist) comes to draw blood. That's a pull — the person doing the work has been pulled and they are “pulling” blood from the patient because it's needed. Now, there might be delays in getting the blood drawn (this would be poor flow), but it's pull. The lab testing is done as a “pull” (we can;t do blood testing in advance on a specimen that doesn't exist) but it might have a long turnaround time (poor flow).
There are times when the emergency department will draw blood (“a rainbow draw,” named for the colors of the different tubes) from a patient “just in case” they are needed. This is “push,” illustrated by the fact that some of those tubes might not be needed. The push, the rainbow collection, is a workaround for slow lab turnaround times. The best fix is reducing the TATs so we can “pull” blood only when needed for the lab.
If a patient needs a bed and there's not a bed available… that's poor flow. There's a mismatch in supply and demand. If the patient is moved once a bed is made available… that's not pull.
A patient getting a same-day primary care appointment when they are sick, that's pull — the patient needs the care, so they get the care quickly. Making a patient wait months for a surgical procedure… that's bad flow.
Restocking supplies to a patient room based on yesterday's usage or a kanban signal… that's pull. A lab with a “standing order” of chemicals and reagents (the same amount every month), that's push. That same lab might have pull if they order a different amount based on usage (a “par level” system) or if they have a kanban system.
An ambulance coming in response to a 911 call… that's “pull.” A slow response time — that's poor flow.
Anyway, I hope this is a helpful discussion. Please add your comments and questions to the post below…
What do you think? Please scroll down (or click) to post a comment. Or please share the post with your thoughts on LinkedIn – and follow me or connect with me there.
Did you like this post? Make sure you don't miss a post or podcast — Subscribe to get notified about posts via email daily or weekly.
Check out my latest book, The Mistakes That Make Us: Cultivating a Culture of Learning and Innovation:
In construction we have the same challenges with understanding pull. One time I observed a team that was creating a collaborative plan that they referred to as “pull planning,” but was actually based on push. At the end of the session I asked our team why they called it a pull plan, and the response I got was “because we have to pull the information out of the sub-contractors.” I had a hard time holding back my smile as I started to work with the team to understand what “pull planning” really is – collaborative planning that starts at the end of the scope of work, planning backwards based on the pull of each internal customer.
Excellent explanation, Mark. The fact that it’s supposed to be the patient pulling from the hospital sounds intuitive in theory, but when you go to map it out on a value stream map it can throw folks for a loop. I found this out the other day when I was in front of a whiteboard trying to draw out this idea of ‘patient pull’ for a team of nursing leaders.
I think in healthcare we’re used to seeing a value stream map showing an inpatient unit (or ICU, OR, etc.) pulling from the ED. This is incorrect, as you pointed out in your post. It’s the patient (or more precisely the patient’s condition with the physician/patient/family acting as the voice of the patient’s condition) that’s doing the pulling. When the patient’s condition is emergent, the patient pulls for emergency care; when the condition transitions to acute, the patient pulls for acute care; etc.
When we correct our value stream maps to reflect true patient pull, we start to see that it’s all about being able to reliably deliver the right level of level when it’s needed to keep the flow going. This mindset begs us to rethink our patient flow metrics, departmental structures, care delivery settings, etc.
Thanks for your additions, Mike.
Thinking of value stream maps, there’s a translation problem into healthcare.
For a manufacturing value stream, part of the flow might be:
Engine Machining –> Assembly
Assembly (to the right) pulls from Machining (on the left) and product moves left to right.
In healthcare, we’d see:
Emergency Dept –> Inpatient Unit
The pull doesn’t come from right to left. It’s from left to right and the patient flow is left to right.
I think this might be part of the confusion?
Yeah, it’s something along those lines. Another way to view it (not sure if this is helpful, but let’s try it on for size):
Emergent Condition –> Inpatient/Acute Condition
In this scenario, the condition of the patient flows left-to-right from emergent –> inpatient/acute –> post-acute.
Instead of a traditional right-to-left pull system, the flow is regulated by the need to get the patient’s condition down a physiological pathway to an end-point of a post-acute and/or preventive state of health. In that sense, it’s one of those non-typical pull systems that would be shown with a weird symbol on a VSM (i.e. “sequenced ball” pull or a FIFO lane).
However, there are traditional pull systems from the main flow (the patient’s condition) down to the hospital resources supplying the care needed at each stage:
Emergent Condition pulls from EMS & ER
Acute Condition pulls from Inpatient/Acute Care
Post-Acute Condition pulls from Rehab or whatever
Not sure if this makes any sense whatsoever :) But thank you for the opportunity to think outside the box for a minute!
I agree that I’m not sure if any of this matters.
That’s why I’ve basically always said, “Who cares about pull vs push?? What matters is improving flow and that means the right care at the right time at the place.”
I do think the patient essentially “pushes” their condition along… the change from healthy to chest pain isn’t pulled by anybody or anything. It just happens… it progresses at its own natural pace, which is what we see with push (or a FIFO lane, etc).
There is also the question of scheduling. In flow the steps proceed one after another in defined sequence. In the conversation above, Mike L. points out that the patient’s condition PULLS services (and supplies). What may be missing in this discussion (I think) is the “go see” scheduling step. There’s an assessment of condition at numerous points which trigger delivery of services and supplies. Not every step, obviously, but many, I think.
Shook and Rother provided the icon for “go see” scheduling in Learning to See but it didn’t appear in any of their examples that I found, and I don’t know that I’ve seen it in any value stream maps (other than the ones I’ve drawn!)
Do you use it in healthcare?
-ALB
I’m not sure if “go see” is a scheduling method as much as it’s an informal method of managing flow real-time? That’s not a term I use.
You’re right that, in healthcare, we can’t “push” work according to schedule regardless of demand like you can in manufacturing. You’re scheduling appointments, but for complex care it seems that the first step in the process is “scheduled” and the rest just flows on its own (or doesn’t).
The flow is often triggered by the downstream resource being available rather than the true true customer need / demand timing.
Mark, perhaps you could elaborate on this topic and discuss the application of forecasting to adjusting supermarket size in advance of expected higher volumes. For example, heavy flooding is expected in the spring, but heavier than expected flooding could be forecast by looking at snowfall amounts, i.e. higher than normal flooding is forecast due to above average snowfall. A pump manufacturer could increase supermarket size in the winter in anticipation. How does this align with the concepts of push and pull and production to a forecast?
Hi Bryan-
Thanks for your question. Yes, a “supermarket” is sized based on a forecast and expected usage of parts between two steps in a process… especially when the upstream process makes lots of different parts that are consumed by the downstream process. The same thinking applies to purchased parts, as well.
Injection Molding –> Supermarket –> Assembly
When I did some work with an auto supplier (this is back in 2003 or so), there was a supermarket of parts. The injection molding machines would make, for example, different types of handles. There are different colors and different molds.
A purely Lean “just in time” model (that’s pretty damn hard to achieve) is “need one, make one.”
Because we don’t have perfect flow, we have a pull system… parts are pulled by assembly from the supermarket and they are pulled by the supermarket (when inventory hits a calculated re-order point) from the molding machines.
Since the molding machines have changeover times, you have to run batches (“single piece flow” isn’t happening). The parts in a batch are being produced faster than the downstream assembly line needs them, so inventory builds up in the supermarket.
Supermarket sizing depends on the expected usage of the parts and the “interval” of production on the molding machine (how often are those parts made… every day, every week?).
“Flow where you can, pull where you must.”
The pull system isn’t ideal, but there are inventory limits that prevent a pure push system from continuing to run and building up inventories.
If your expected usage (your forecast) goes up for some reason (or adjusts seasonally), you’d want to adjust the size of your supermarket accordingly.
Does that help?
Yes, it makes good sense. Some “lean thinkers” denounce production to a forecast, but sometimes it makes sense. Yes, there is risk of overproduction, but there is also risk of failing to meet demand, too, if your supermarket is sized to average demand. Increasing supermarket size per forecast then needs to be mitigated by adjusting production to the actual rate of demand and “underproduce” in order to adjust supermarket size down to actual demand. Does that make sense?
I learned from a Japanese consultant once:
1) first job is making customer schedule
2) second job is low inventory
You’re right, there’s risk of too much inventory and risk of too little.
The best strategy is to work continually to reduce setup/changeover times, which allows you to produce smaller batches, which means less inventory without jeopardizing customer deliveries.
With a supermarket, if you’re in a mode of increasing the inventory levels, your weekly production goal would be demand PLUS the amount required to increase inventory.
If you’re resizing the supermarket lower, then you produce LESS than demand to allow that inventory to shrink.
I work in healthcare, but I have experience in manufacturing from previously working at my father’s small contract manufacturing business. Because we are a contract manufacturer, we only produce finished goods based on pull and we only order parts (if we are out of stock) once the customer has delivered a PO. However, most of our suppliers require us to fulfill large Minimum Order Quantities. How would you classify this scenario where our customer may only require 25 parts, but our supplier requires us to buy 500? It is a pull strategy that affects our business like a push scenario. Over production and high inventory levels ensue.
Colin, what you describe sounds like pull (you are trying to order what you need based on real demand and usage) but you’re saddled with unfortunately high minimum order quantities. That’s what being a small manufacturer gets you… you don’t get the best terms from bigger suppliers (and probably also have demanding customers). The high inventory levels aren’t due to “push,” but from having a supplier that’s not willing to work with you as best as they could… if they can’t sell and ship smaller quantities in a profitable way, they have their own process improvement opportunities to work on!
[…] #Lean: Clarifying Push, Pull, and Flow in a Hospital; the Patient “Pulls” (1735 views) […]
[…] #Lean: Clarifying Push, Pull, and Flow in a Hospital; the Patient “Pulls” (1953) […]
Well said. It goes back to the supply and demand thing that allows continuous flow of the value from the supplier to the customer who pays for the value (product or service) provided by the business enterprise as needed and when needed.
Good explanations Mark! Adding to this, we often don’t have the right measurement systems and incentives aligned with a pull system. If people are not measured and incentivized for “Pull” we are expecting them to do the work out of the goodness of their heart and only after they truly understand the concepts of “push” vs. “pull” (which you also agree is not well understood). As an example, most health system batch radiology results to a queue that radiologists sit and review one at a time when they get to it. This obviously creates delays in patient stays waiting on a radiology read in the ED, Urgent care, etc. In another example, where incentives are correctly aligned, multiple radiologists are logged into a store-and-forward type tele-med system. The first radiologist to open and read the x-ray is paid for doing that work. Here they are all in competition to get to the result as quickly as possible. In that system, radiology reads had less than 10 minute turn-around times! Developing processes that contain a built in pull process, with measurements and incentives that create it seem to be ideal. People start performing their work with a pull process and they don’t even know they are doing it. :)