Mark's Note: Today's guest post is by Christina Kach, who I met via Twitter and email. I'm hoping this will be the first in a series of posts geared toward young Lean and continuous improvement professionals, but I think there are lessons and good reminders for all of us, regardless of our age.
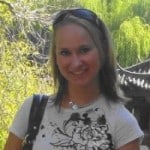
Pop quiz: Do you know the best time to catch the shortest lines at Walt Disney World? During a family trip in the 4th grade, I figured it out by studying the travel guide, observing park behavior, and mapping out routes on the Magic Kingdom pamphlet. (I'll share my secret, the answer: during a parade). I believe those out there like myself, with minds and enthusiasm for processes improvement – the Industrial Engineers, Lean practitioners, continuous improvement leads, and Six Sigma gurus of the world – are born this way (and likely figured it out years before we studied it in school).
After college graduation in 2009, I was fortunate to land a job where I am able to incorporate my passion for process improvement. In the time since, I've learned a few things I'd like to share – to motivate the next generation of Lean thinkers.
You're Not in College Anymore
Hear the reality check now, before you start your first “real world” job. It isn't all about you anymore. It WAS all about you; your grades, your extracurricular activities, your weekend plans. Now it is about the team, the department success, and the goals of the company. Furthermore, there is no course outline or syllabus of expectations and due dates to help you navigate week to week. It is on you to map the work on your own.
Make it Personal
If there is one thing you do not want to be known for in your career (I speak from experience), it is to be “that guy” who only comes to talk when he needs something from you. Getting to know your new coworkers is #1. What is their passion? Travel, their children, cooking? (Hint: try looking around their cubicle). The reverse is also true; share your interests with people and have a few pictures in your work space to prompt conversations. Don't just “hear” to give the impression you are paying attention – really LISTEN. Be truly engaged with your team, getting to know them, learning from them, and asking questions. And here's the kicker: you can't just do it once and be done. You have to follow up, build the relationship, and nurture the connection.
Attitude
There are many factors in a job you can't control – so focus on the ONE variable that you can à your own attitude. Your own attitude affects interactions, overall demeanor, and motivation – try to keep it positive. On any given day you can make the decision to be happy or cranky. You can react poorly to criticism or you can say to yourself, “well I've figured out what NOT to do.” Attitude isn't one size fits all; you must adapt your interactions with each person. As time goes by, you'll learn what works best in each situation. This is a topic worth finding guidance on from a coach or mentor.
Engagement
You were hired to solve problems. Sitting at your desk and waiting for problems to show up looking to be solved isn't the way. Keep an ear out for opportunities and speak up – “I can help with that.” Talk to your teammates and your boss. Just keep this in mind: how can I help? While I don't have an exact solution on how to go about this, adapt according to your specific situation, I do know that sitting around waiting for a project to appear is NOT going to work.
Lean doesn't have to be in a formal job title for you to apply it to your work or pursue it as an interest. If you see an opportunity for improvement, work it. If there is a formal “Lean” member of the team, bring it up. Or take the improvement ideas to your manager. Just remember to go in with a solution for the problem, not just to complain about the problem.
The ideas I've talked about here may seem unnatural at first. Like an athlete in training, continue to practice these skills, they will strengthen over time. No matter what the naming convention – Lean, Six Sigma, operational excellence – the theme is the same: continuous improvement. The same goes for your career: continually reach out to your team, learn, engage, and persevere on those frustrating days.
Christina invites you to connect with her via Twitter (@ChristinaKach) and her blog for young professionals – “Catch Careers.”
What do you think? Please scroll down (or click) to post a comment. Or please share the post with your thoughts on LinkedIn – and follow me or connect with me there.
Did you like this post? Make sure you don't miss a post or podcast — Subscribe to get notified about posts via email daily or weekly.
Check out my latest book, The Mistakes That Make Us: Cultivating a Culture of Learning and Innovation:
I enjoyed reading. Maybe it’s not all about the $$ after all. Thanks Christina & Mark.
Good inputs. There are more and more recent grads who were exposed to lean in college who are entering the workforce as fully-committed change agents. That’s great to see. I believe it’s making a difference.
I particularly love the first bit of advice – it’s not about you, it’s about the team. I think some recent grads take a few years to realize this. This doesn’t mean putting in your time just for the sake of putting in your time. It just means that your contributions are not defined by your own successes but by the team’s.
One I’d like to add, that’s lean specific, is that even though you learned lean in college, doesn’t mean that any of that is the right knowledge you need to apply it. I don’t want to, or mean to, degrade the effort that professors have done to integrate lean into the curriculum. We have done a lot to help that happen. But professors have a job to do: teach the theory, the history, the models, the math. That’s all useful, and is necessary, but also insufficient. I never want to hear the words “I learned lean in college” again – you learned ABOUT lean. You learn lean by doing it – period.
Welcome Christina to the lean blogging world, and the lean change agent world.
Thanks again to Christina and thanks for your comments, guys.
Jamie – yes, I agree that “learned” shouldn’t be past tense, especially with Lean. You don’t “learn lean” in a college class, a four-day class, or a single project (or from a single book). Early in my career, I learned a great lesson from a grizzled old Lean guy at a major auto supplier when he introduced himself to the team and said “I’m Jim and I’ve been learning Lean for 25 years.”
We’re all always learning and improving our understanding and practice of Lean principles.
Welcome to the Blog Christina:
Similar story, my first summer job during college I was given the task of meticulously copying a stack of front-and-back half sheets of paper on to full-size card stock, then cutting them in half, assuring everything was in the correct orientation. I was told that I couldn’t use the auto feeder because it would jam, and it was too easy to “waste paper” if you set it up wrong.
As soon as the boss left the room, I was figuring out how to line up the sheets in the auto-loader. I did a week’s work in about 15 minutes. Thankfully, they found more for me to do that summer.
-Andy
Andy, way to challenge the “way it has always been done” and come up with a great solution! Continous Improvement doesn’t have to be all about deep, long term projects. Quick hitters of “this could be better” are just as impactful in their own way.
Jamie, that is a great insight. Adapting the methodologies & techniques that are learned in a classroom or book are only the begining. You don’t fully understand the concepts until you apply it to real world solutions and see first hand the benefits.
Thank you for the warm responses to my guest article!
Take Care,
Christina
As a no-longer-young person with a lot of time in workplaces with different cultures, plus knowing and learning from people like Jamie and Mark, plus dozens of people in manufacturing, lean or not, let me add some observations.
People right out of college are often looking for the grade or the promotion to the next level — just what happens after 16+ years of school. Get over it.
That said, I believe it was Jamie who said that the difference between the younger people in lean and the older ones is that they grew up in lean (if they were lucky). They didn’t have to unlearn one thing and learn another. As accomplished as they are, I meet a lot of very experienced lean guys who don’t breathe lean attitudes outside of the workplace. They don’t truly get the concept of respect for people — intellectually maybe, but not in their gut. You will work with people like this, and it will make it harder. But don’t let yourself overlook how much you can learn from them before they head for the pack of retiree consultants. They may be grizzled or think and talk a little more slowly than you, but you need their teaching and mentoring.
Our generation thought we would change the world. We thought we were more open to diversity and new ideas. Now we look more rigid and inflexible. But you should have seen the generation before us!
Christina and Jamie have great advice. I’m counting on you younger people to make lean a reality where it has been more of an idea or a tool. Go for it!
Very insightful Christina, some change agents don’t learn those lessons so quickly. The position is very much about influence and credibility so you have to learn to connect with people as you rightly point to the value.
I came from the shop floor environment so you learn the importance of the team very quickly, usually in a harsh way! I find team bonding becomes less the further up an organisation you get which is unfortunate.
Good luck with your career.
Steve.
Parades! Yes I was a little older but figured out the same thing. My parents always gave me the map of any place we went to see if I could figure out a better way. I thought it was because I was creative enough to figure it out. Later I learned it was to teach me to problem solve. My dad was a Lean guy before it was Lean. After a couple of trips to Japan, he noticed the culture and brought some of that home with him.
Having worked in many different environments it is not just the people you need to get to know but the culture. You almost have to be part psychologist and part Historian along with being change agent. I am a people person that can talk to anyone. I enjoy finding out about them. The more you engage people the more they will open up. Even those that are like brick walls. Once you find out what interest they have use that to get to know them better. Sometimes it takes a little research to find information about that interest, but they will appreciate you taking time to find out more about what they like.
The Culture part can be a shock at times. I face that daily in my current position. I stay positive and walk away when I need to. I am chiseling away at it one improvement at a time getting others to glance in the direction of lean. “That’s the way we have always done it” is the current Moto. 70 years it has worked why change?
Thanks Christina and Mark
This is a wonderful post and I look forward to more.
[…] 2012 · 0 comments Mark’s Note: Here is the second guest post from Christina Kach. Read her first contribution here. Today’s post builds on last week’s “Chuck Norris” meme post. And see more […]
[…] in the world. We also see people entering the workforce as ready-to-go lean change agents, such as Christina Kach who just started blogging on Mark Graban’s blog.Why is all of this […]