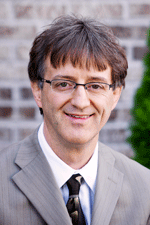
Joining me for episode #187 is Joe Swartz, my friend and esteemed co-author of our books Healthcare Kaizen: Engaging Front-Line Staff in Sustainable Continuous Improvements and The Executive Guide to Healthcare Kaizen: Leadership for a Continuously Learning and Improving Organization. You can learn more about our books here.
Joe is Director of Business Transformation at Franciscan St. Francis Health System in Indianapolis (his full bio is here). In the episode, we talk about his background with Kaizen and how he got into healthcare. Joe discusses how Franciscan got started with Kaizen, some of his favorite Kaizen examples, why it would have taken too long to engage everybody through Lean Six Sigma projects, what they are teaching managers about leading in a Kaizen culture, and the work that still needs to be done in their cultural transformation.
For a link to this episode, refer people to www.leanblog.org/187.
For earlier episodes, visit the main Podcast page, which includes information on how to subscribe via RSS or via Apple Podcasts.
You can also listen via Stitcher.
Podcasts Sponsored by KaiNexus
If you have feedback on the podcast, or any questions for me or my guests, you can email me at leanpodcast@gmail.com or you can call and leave a voicemail by calling the “Lean Line” at (817) 372-5682. Please give your location and your first name. Any comments (email or voicemail) might be used in follow ups to the podcast.
Podcast Summary
You can also read and download this 4-page PDF summary of the podcast:
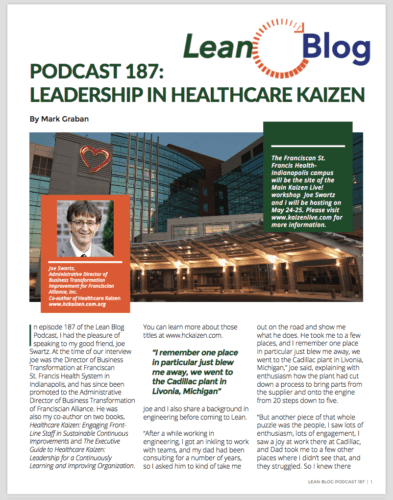
How to Create a Culture of Continuous Improvement in Healthcare
In episode 187 of the Lean Blog Podcast, I had the pleasure of speaking to my good friend, Joe Swartz. Joe is the Administrative Director of Business Transformation at Franciscan St. Francis Health System in Indianapolis, and is my co-author on two books, Healthcare Kaizen: Engaging Front-Line Staff in Sustainable Continuous Improvements and The Executive Guide to Healthcare Kaizen: Leadership for a Continuously Learning and Improving Organization. You can learn more about those titles at www.hckaizen.com.
Joe and I also share a background as engineers who started our careers in manufacturing. In those early experiences, Joe learned about the power of engaging everybody in improvement.
One company that stood out was Spraying Systems, a metal forming plant in Chicago that makes spray nozzles. There, Joe and his father experimented on how to engage all employees.
Joe said, “The president there really pushed the engagement of all employees, he wanted all employees engaged in implementing Lean.”
Around 2005, Joe transitioned into healthcare, starting when some Purdue professors were helping St. Francis hospital get started with a Lean Six Sigma program. The professors were knowledgeable about Six Sigma, but were looking for someone who knew Lean. Joe filled that gap and the team worked on bringing their program not only to St. Francis hospital, but to all the Franciscan alliance hospitals in Indiana and Illinois.
“I knew from my previous experiences, that at some point I needed to engage all employees to really get my job done,” Joe said.
“We were doing Lean Six Sigma projects at the time and we could do maybe 10 a year, and you can engage 15-25 people per project, I looked out to the future and it would take 20 years or 30 years to reach every employee. So I really needed something that would engage every employee, starting right away.”
Joe said that he took the concepts in Norm Bodek's book The Idea Generator, which spelled out how to dramatically simplify engaging an employee, and tried to simplify them even further. In April of 2007, Joe brought Norm in to meet with senior management for an hour and then have him speak to a larger group of about 250 people, for three hours about what “Quick and Easy Kaizen” is all about. These talks kicked off St. Francis' Kaizen program, which launched the next day.
One type of improvement that Joe said was his favorite is the simple improvements made at the beginning of the process. Joe explained that he asks all employees to begin with something they can control themselves, rather than trying to change other people. Once they've gotten better, then they can move on to changing the workplace, patient, and hospital.
Joe regularly chooses notable Kaizens and communicates them back to staff. He chooses Kaizens that carry the message of combining good for staff, good for patients, good for families, good for the community, and good for the hospital. Joe said that after a while, staff really began to pick up on what type of Kaizen is really celebrated and began submitting more Kaizens of that type. The effect has been the culture shift toward improvement that is needed.
Joe also contributed leadership to the success of culture change, saying, “The departments that do really well are run by leaders who are passionate about Kaizen. Anything they do to drive home the importance of Kaizen, and message it back to their employees drives Kaizen.”
“If the employees see managers making it important, it's important to staff,” Joe said. “They're always asking, and messaging, and making it a priority in their agenda; they're always talking about it.”
While constant communication is important for Kaizen, when I asked Joe about the role of the manager in helping the employee implement Kaizen, it brought an example to his mind. Joe said that, a few months before our interview, he had a new manager come to him to raise concerns about the amount of time Kaizen was demanding of her, as it was taking up about one day in each week. When Joe questioned her about the problem, it became clear that she was following up with each Kaizen herself.
“What you got to do is turn that around. As manager, you shouldn't take on any of the work, you should coach them, for them to take on the work. So after she shifted that back onto them, it freed up all kinds of time for her to focus on the future and it empowered the employees to figure out how to do the work,” Joe said.
“It's a little rough at first, but they learn; and this is all about developing people. We're developing a culture of continuous improvement.”
Joe said the managers who are able to coach their staff to do the work of improvement themselves all find that they have more time to focus on what they should be focusing on, which is developing the future. He also said that while staff time to do the work of each Kaizen may at first be tight, he also finds that time opens up for staff, as well.
“If the manager can trust the process and find the time for staff somehow, it might take a couple of months, but they will start to find that there's extra time for people to work on stuff like this. I've seen it in department, after department, after department, at our hospital and other hospitals that have adopted this,” Joe said.
Having been impressed with the implementation and culture development at St. Francis, and to touch on the themes in our book The Executive Guide to Healthcare Kaizen: Leadership for a Continuously Learning and Improving Organization, I asked Joe what key things his senior leaders do to foster the culture of Continuous Improvement. He said that his leaders believe in it and convey that belief through their messaging.
“Our CEO, at one of the recent all-employee meetings, I counted and I think it was five times that he mentioned Kaizen. So it's still important to them, and they convey that,” Joe said.
“And they give us time they give me and my staff time at important meetings to talk about Kaizen. They still fund the program, they give our staff some of the best and the brightest in the organization to work in our department. And they allow us to experiment, we're still trying new things and learning new things.”
To wrap up, I asked Joe what he anticipates doing in the future to increase participation. Joe said that he keeps it positive, not talking about the low-performers, but lifting the high-performers and departments up to keep the momentum and energy high.
“Really it's all about creating that culture, so doing whatever it takes to create that culture where all our employees are engaged everyday in the search, the search for how do we make this better, how do we this little thing better, and this little thing better,” Joe said.
“And that is going to make us much more competitive, make everybody's job more secure, and provide better care for our patients and their families, which is what we're all really trying to do.”
Please scroll down (or click) to post a comment. Connect with me on LinkedIn.
Let’s build a culture of continuous improvement and psychological safety—together. If you're a leader aiming for lasting change (not just more projects), I help organizations:
- Engage people at all levels in sustainable improvement
- Shift from fear of mistakes to learning from them
- Apply Lean thinking in practical, people-centered ways
Interested in coaching or a keynote talk? Let’s talk.
Join me for a Lean Healthcare Accelerator Trip to Japan! Learn More
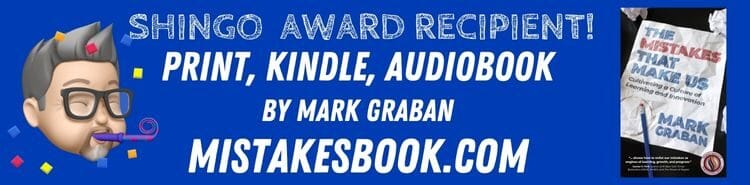
[…] be a regular contributor in the future and I’ll be doing a podcast with him soon (update: listen here) about his experiences at the Franciscan St. Francis Health System. Also, check out this video […]
Comments are closed.